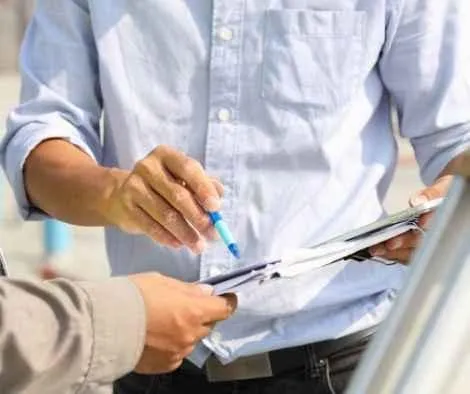
Accident Prevention in Construction: Team Program Plan!
Accidents on construction sites are not just costly—they can change lives in an instant. When teams are armed with a clear and practical accident prevention program, the work environment becomes safer, and productivity improves.
In this guide, we break down how to build an effective safety plan that meets key regulations, supports team efforts, and keeps construction sites secure.
Whether you are a site manager or a safety officer, this post will give you step-by-step instructions on developing an accident prevention plan that aligns with OSHA and USACE requirements. Read on to learn the basics of accident prevention in construction, key plan components, and practical strategies for keeping your team safe every day.
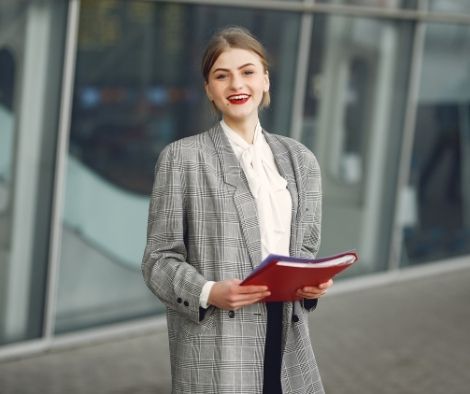
The Importance of a Safety Program on Construction Sites
Construction sites are busy environments where many factors can contribute to accidents. Without a comprehensive accident prevention program, teams may struggle with unclear safety procedures and an increased risk of incidents. A solid plan:
Reduces the likelihood of injuries: When every team member understands the safety protocols, fewer accidents occur.
Supports regulatory compliance: Meeting OSHA and USACE guidelines is essential for legal and operational reasons.
Improves productivity: Fewer accidents mean less downtime and a more confident workforce.
Fosters a culture of safety: A clear safety plan signals to everyone that their well-being is a top priority.
Creating a successful accident prevention program for teams is a vital part of managing construction sites. A well-crafted plan not only safeguards your crew but also upholds the standards expected in the construction industry.
Understanding the Basics of Accident Prevention in Construction
Accident prevention in construction is the practice of designing and implementing safety measures that protect workers from harm. It involves planning for various risks, communicating effectively, and making safety a shared responsibility.
Here are the key elements:
Defining the Safety Plan
An accident prevention plan is a written document that outlines procedures, responsibilities, and actions to reduce accidents on construction sites. It should be clear, actionable, and easy for everyone on your team to follow.
Why It Matters
Lives and well-being: The primary goal is to safeguard workers.
Legal compliance: Adhering to accident prevention plan OSHA guidelines and USACE Accident Prevention Plan Requirements is not optional.
Financial benefits: Reducing accidents lowers insurance costs and avoids work stoppages.
Reputation: A strong safety record attracts skilled workers and reputable contracts.
By ensuring that your accident prevention plan is comprehensive, you create a framework that protects everyone on the job site and sets the stage for a secure working environment.
Key Components of an Accident Prevention Plan
A successful accident prevention plan includes several critical components. Each part works together to create a seamless safety system.
Risk Assessment and Hazard Identification
Start by identifying all potential hazards on the construction site. This involves:
Site Walkthroughs: Regular inspections help spot unsafe conditions.
Worker Feedback: Encourage team members to report hazards.
Historical Data Review: Analyze past accidents and near misses.
Pro Tip: Create a risk assessment checklist that includes equipment, environmental factors, and human error possibilities. A clear record can help you stay ahead of potential issues.
Clear Procedures and Responsibilities
Your plan must outline procedures for:
Emergency Response: How to handle accidents when they occur.
Daily Operations: Safe practices that every team member must follow.
Equipment Use: Proper training on tools and machinery.
Assign clear roles and responsibilities so that every worker knows who to approach for guidance or in case of an emergency.
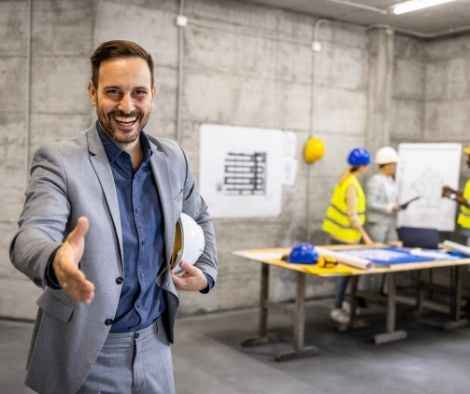
Training and Communication
Ongoing training is essential to keep everyone informed. Schedule regular safety meetings and refresher courses. Use multiple formats—hands-on training, written guides, and visual aids—to communicate safety procedures effectively.
Equipment and Protective Measures
Ensure all workers have access to the necessary personal protective equipment (PPE). Regularly check that machinery is in good working order and meets safety standards.
Regular Inspections and Audits
Implement a routine inspection schedule. Regular audits help identify gaps in the accident prevention plan and ensure that safety protocols are consistently followed.
Accident Prevention Plan OSHA and USACE Guidelines
Compliance with OSHA standards and USACE guidelines is a critical part of any safety plan.
Here’s how to meet these requirements:
OSHA Requirements
OSHA’s regulations provide a framework for ensuring worker safety. When developing your accident prevention plan:
Review OSHA Standards: Understand the guidelines relevant to your construction site.
Document Procedures: Keep a detailed record of safety procedures and training sessions.
Report Accidents: Follow OSHA’s protocols for reporting incidents.
USACE Accident Prevention Plan Requirements
USACE has its own set of standards for accident prevention plans. These include specific templates and checklists that help ensure compliance. When building your plan:
Use a USACE Accident Prevention Plan Template: These templates are designed to cover all necessary aspects of site safety.
Follow the USACE Accident Prevention Plan Checklist: This checklist will guide you through each step of the process.
Understand USACE Accident Prevention Plan Requirements: Regularly review updates to ensure your plan remains current.
Adhering to these guidelines not only keeps you compliant but also builds a safety culture that protects every team member.
Steps to Develop a Comprehensive Accident Prevention Program
Creating a detailed accident prevention program involves careful planning and team collaboration. Follow these steps:
Establish a Safety Committee
Form a group that includes management, safety officers, and workers. A diverse team ensures all viewpoints are considered when developing the plan.
Conduct a Detailed Site Analysis
Examine your construction sites to identify potential hazards. Consider factors like:
Site layout and access points
Weather conditions and environmental risks
Equipment and material storage areas
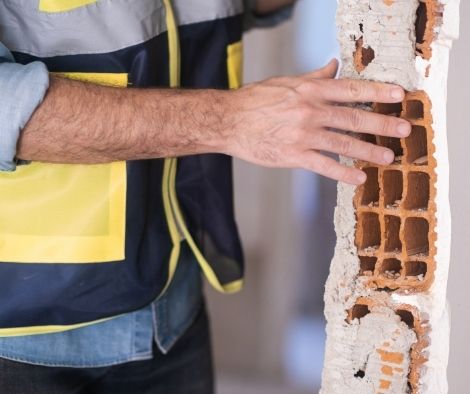
Develop a Customized Accident Prevention Plan
Based on your analysis, write a plan that outlines specific safety measures. Include:
Detailed procedures for each identified risk
Responsibilities assigned to each team member
Emergency contact information and protocols
Integrate Regulatory Guidelines
Ensure that your plan meets both Accident Prevention Plan OSHA standards and USACE Accident Prevention Plan Requirements. Use available templates to structure your document clearly.
Create Supporting Materials
Develop training materials, signage, and checklists to support your accident prevention program. Resources like the USACE Accident Prevention Plan Template and USACE Accident Prevention Plan Checklist are valuable tools in this process.
Test and Revise the Plan
Run simulations or safety drills to test your procedures. Gather feedback from your team and adjust the plan as needed.
Implementation Strategies on Construction Sites
Once your accident prevention plan is written, implementation is key. Here’s how to put your safety plan into action on construction sites:
Communicate the Plan to the Team
Hold a Kick-Off Meeting: Introduce the safety plan and review key points.
Distribute Copies: Ensure every worker has access to the plan.
Display Signage: Post critical safety instructions in common areas.
Provide Hands-On Training
Practical training sessions help workers understand how to use equipment safely and respond to emergencies. Include:
Toolbox Talks: Short, focused sessions on specific safety topics.
Simulation Drills: Practice emergency response procedures.
Monitor Compliance and Performance
Set up a schedule for regular safety inspections and audits. Use the USACE Accident Prevention Plan Checklist to verify that all safety measures are in place.
Foster a Culture of Open Communication
Encourage workers to report hazards or suggest improvements without fear of reprisal. Regular safety meetings can help maintain an open dialogue.
Training and Communication Best Practices
Training is a continuous process in accident prevention.
Here are some best practices:
Regular Refresher Courses
Safety training should not be a one-time event. Schedule regular sessions to update workers on new risks and procedures.
Use Multiple Learning Methods
Different team members learn in different ways. Mix in-person training, video demonstrations, and printed materials to cover all bases.
Keep Training Practical
Focus on realistic scenarios that workers may face on construction sites. Practical demonstrations help cement the information.
Track and Document Training Sessions
Maintain records of who has completed safety training. This documentation is useful for audits and regulatory reviews.
Pro Tip: Use a simple log sheet for training sessions. This ensures that no one is left out and that each session is recorded accurately.
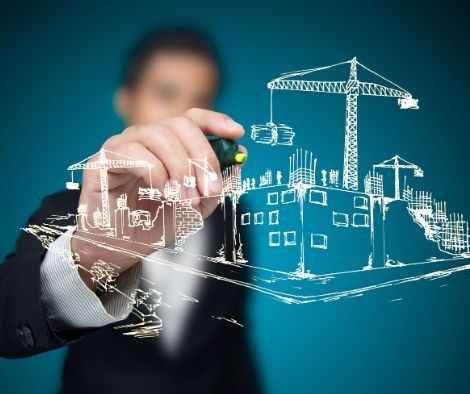
Tools and Resources for Accident Prevention
A wide range of tools and resources is available to support your accident prevention program. Here’s a look at some valuable assets:
Templates and Checklists
Accident Prevention Plan Template: Helps structure your safety plan.
USACE Accident Prevention Plan Template: Provides a format that meets USACE requirements.
USACE Accident Prevention Plan Checklist: Ensures all necessary steps are covered.
Software Solutions
Consider software that tracks safety compliance, incident reports, and training schedules. Many solutions allow you to customize reports for OSHA reviews.
Industry Publications and Guides
Stay updated with the latest safety standards and best practices by following industry publications and attending safety conferences.
On-Site Tools
Invest in tools that support daily safety routines:
PPE Stations: Easily accessible locations for personal protective equipment.
First Aid Kits: Well-stocked and readily available.
Communication Devices: Radios or mobile phones for rapid emergency contact.
Real-World Examples and Case Studies
Understanding how other teams have successfully implemented accident prevention programs can provide valuable insights. Below are a few examples that illustrate different approaches:
Construction Company A: A Proactive Approach
Company A implemented a thorough accident prevention plan that involved:
Regular Training: Weekly toolbox talks and monthly full-scale drills.
Worker Involvement: A safety committee that met bi-weekly to review site conditions.
Compliance Reviews: Frequent audits using a customized checklist based on USACE Accident Prevention Plan Requirements.
As a result, Company A reduced on-site injuries by over 40% in just one year. Their safety plan was praised for its clarity and ease of use, showing that practical steps lead to real improvements.
Construction Company B: Integrating Technology
Company B invested in a digital safety management tool that:
Streamlined Communication: Enabled real-time updates on safety protocols.
Automated Inspections: Scheduled and tracked routine inspections.
Customized Reporting: Generated reports that met Accident Prevention Plan OSHA standards.
This integration not only improved safety outcomes but also saved the company time and reduced administrative burdens.
Construction Company C: Fostering a Safety Culture
Company C focused on building a culture where every worker took personal responsibility for safety:
Open Communication: Encouraged reporting of hazards without fear of punishment.
Peer-to-Peer Training: Seasoned workers mentored new hires.
Reward Programs: Recognized individuals and teams that contributed to improving safety.
Their emphasis on culture led to fewer accidents and a noticeable improvement in overall morale.
Common Pitfalls and How to Avoid Them
Even the best plans can face challenges during implementation. Here are some common pitfalls and strategies to avoid them:
Lack of Team Involvement
Pitfall: If workers feel that the safety plan is imposed from above without their input, they may be less likely to follow it.
Solution: Involve team members in developing and reviewing the accident prevention plan. Their practical experience can identify hazards that management might overlook.
Infrequent Updates
Pitfall: A plan that isn’t reviewed regularly can quickly become outdated, especially in dynamic construction environments.
Solution: Schedule periodic reviews and revisions of the safety plan. Update the USACE Accident Prevention Plan Checklist as new risks are identified.
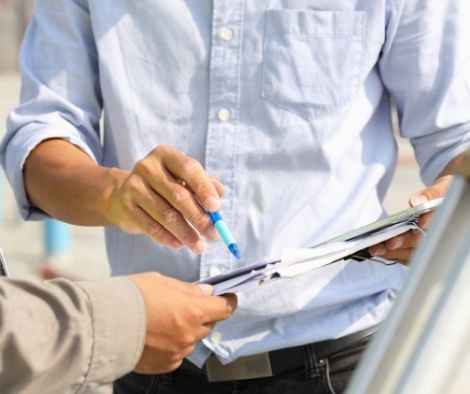
Overcomplicating Procedures
Pitfall: A safety plan filled with technical jargon and overly complex procedures may confuse rather than help.
Solution: Write the plan in clear, simple language. Use diagrams, tables, and flowcharts to explain processes where possible.
Inadequate Training
Pitfall: Without regular, hands-on training, workers might not remember or understand safety protocols.
Solution: Invest in ongoing training sessions and ensure that practical demonstrations are part of the curriculum.
Maintaining and Reviewing Your Accident Prevention Program
Creating the plan is only the first step. To keep your construction sites safe, continuous improvement is essential.
Regular Reviews
Monthly Meetings: Hold safety meetings to discuss any incidents or near misses.
Quarterly Audits: Conduct formal reviews of safety procedures and compliance with OSHA and USACE standards.
Annual Updates: Revise the accident prevention plan at least once a year to incorporate new regulations and feedback.
Continuous Feedback
Encourage all team members to share their experiences and suggestions for improvement. Use feedback forms or a suggestion box to capture insights.
Documenting Changes
Keep a log of updates made to the safety plan. This record is useful during inspections and helps track progress over time.
Pro Tip: Establish a simple digital log that allows you to record changes and feedback in real time. This ensures that improvements are documented and that everyone is aware of the latest procedures.
Measuring the Success of Your Safety Plan
How do you know if your accident prevention program is working? Monitoring key performance indicators (KPIs) is essential.
Key Metrics to Track
Incident Rates: Monitor the number of accidents and near misses.
Training Participation: Keep track of attendance at safety sessions.
Inspection Scores: Use audits to assess compliance with safety procedures.
Worker Feedback: Regular surveys can gauge how safe employees feel on the job.
Analyzing Data and Adjusting
Regularly analyze your KPIs and compare them against industry benchmarks. Use this data to adjust the safety plan where necessary.
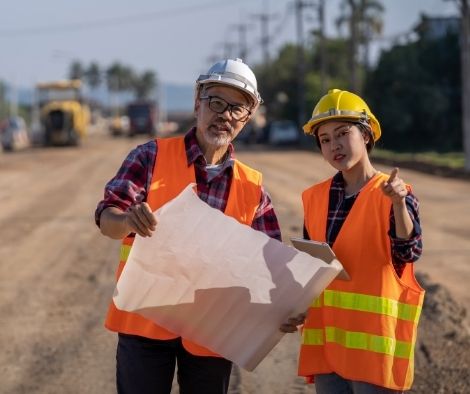
The Role of Leadership in Safety
Strong leadership is the backbone of any accident prevention program. Leaders must set the tone and be visible examples of safety commitment.
Leading by Example
When management adheres to safety protocols, workers are more likely to follow suit. Ensure that everyone from supervisors to site managers practices what they preach.
Open and Honest Communication
Create an environment where questions are welcomed, and issues are addressed promptly. Leaders should be accessible and proactive in addressing safety concerns.
Recognizing and Rewarding Safe Behavior
Positive reinforcement can drive improvements in safety performance. Acknowledge those who consistently follow the plan and contribute to a safer work environment.
The Path to Safer Construction Sites
A successful accident prevention program is a living document—one that grows and evolves with your team’s needs and the construction site environment. By developing a clear accident prevention plan that meets OSHA and USACE requirements, you are taking significant steps to ensure that every worker goes home safe at the end of the day.
Remember, creating a safety plan is not a one-time task. It requires ongoing effort, regular updates, and the commitment of every team member. With the right tools, clear communication, and consistent leadership, your construction sites can become models of safety and efficiency.
Final Thoughts
Safety is not just a checklist item—it is an ongoing commitment to every individual on the construction site. A well-planned accident prevention program protects lives, meets regulatory standards, and builds a strong foundation for success.
Now is the time to review your current safety measures, update your accident prevention plan, and involve your team in the process.
If you’re ready to take the next step, visit PlanTheJob.com to access our proven solutions, templates, and expert guidance. Start building a safer work environment today—your team deserves it!