
Contractor’s Guide to Developing Quality Control Plans
In the construction industry, delivering top-notch projects isn't just about meeting deadlines and budgets—it’s about ensuring quality at every step. A well-crafted Quality Control Plan (QCP) serves as the backbone for achieving this goal, guiding contractors through structured processes that guarantee each project meets or exceeds client expectations.
It provides a clear framework for monitoring workmanship, verifying materials, and addressing potential issues before they escalate, ultimately reducing costly rework and delays.

An effective Quality Control Plan goes beyond simple checklists; it establishes clear quality benchmarks, defines accountability, and fosters a proactive approach to problem-solving. By integrating Key Elements of Quality Control Plans—such as inspection protocols, testing procedures, and corrective actions—contractors can maintain consistency, meet regulatory requirements, and uphold the highest construction standards.
Additionally, a well-documented QCP serves as a point of reference for the entire team, ensuring that every phase of the project aligns with industry best practices and client expectations.
Developing a Quality Control Plan requires careful planning and a commitment to continuous improvement. It involves assessing project specifications, setting measurable quality standards, and training personnel to follow established guidelines.
A Design Quality Control Plan is equally essential, as it ensures that architectural and engineering details are thoroughly reviewed before construction begins, minimizing design errors and improving overall project efficiency. By prioritizing quality control from the start, contractors can deliver projects that are not only structurally sound but also built to last.
What Is a Quality Control Plan?
A Quality Control Plan is a comprehensive document that outlines the procedures, processes, and responsibilities necessary to ensure that a construction project meets specified quality standards. It serves as a roadmap for contractors, detailing how to manage and control various aspects of the project to achieve the desired quality outcomes.
By establishing clear guidelines, a QCP helps maintain consistency, minimize errors, and ensure that every phase of the project adheres to industry regulations and client expectations.
A well-structured Quality Control Plan includes detailed inspection protocols, material verification processes, and clear accountability for every team member involved. It provides a systematic approach to identifying potential issues early, allowing contractors to take corrective action before minor defects turn into costly problems.
Regular monitoring, documentation, and continuous quality assessments are essential components that support a smooth construction process and prevent delays caused by rework.
Additionally, a Quality Control Plan promotes communication and collaboration among project stakeholders, ensuring that all parties—contractors, subcontractors, and suppliers—are aligned with quality expectations.
By integrating best practices, adhering to strict quality standards, and maintaining thorough documentation, contractors can enhance efficiency, reduce risks, and deliver high-quality results.
In essence, a strong QCP is not just a document but a proactive strategy that drives successful project execution and long-term client satisfaction.
Why Is a Quality Control Plan Essential?
Implementing a Quality Control Plan (QCP) is crucial for several reasons:
Client Satisfaction:
Ensures that the finished project aligns with the client’s quality expectations. A well-documented QCP establishes clear performance standards and benchmarks, reducing discrepancies and ensuring that the final outcome meets or exceeds contractual obligations.
Satisfied clients are more likely to provide positive referrals and repeat business, making quality control a key factor in long-term success.
Regulatory Compliance:
Helps in adhering to industry standards and legal requirements. Construction projects must meet strict guidelines set by regulatory bodies, and failure to comply can result in fines, legal disputes, and project shutdowns.
A robust QCP ensures that materials, workmanship, and safety standards align with local and international building codes, reducing the risk of non-compliance issues.
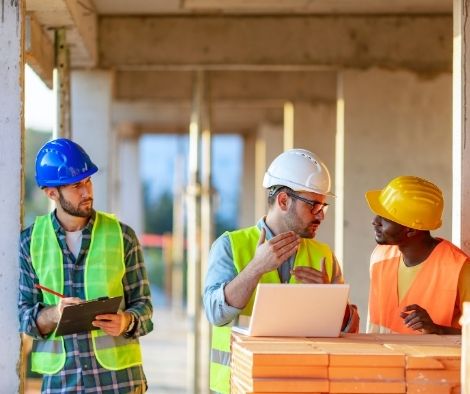
Risk Mitigation:
Identifies potential issues early, reducing the likelihood of costly rework or delays. By incorporating detailed inspection protocols and proactive monitoring, contractors can detect and correct defects before they escalate into major setbacks. This reduces unnecessary expenses, minimizes delays, and improves overall project efficiency.
Continuous Improvement:
Provides a framework for ongoing assessment and enhancement of construction processes. A well-structured QCP encourages regular evaluations, data-driven decision-making, and training initiatives to refine quality standards. By fostering a culture of continuous improvement, contractors can enhance efficiency, reduce waste, and consistently deliver high-quality projects that stand the test of time.
Key Elements of Quality Control Plans
A robust Quality Control Plan (QCP) encompasses several critical components:
1. Quality Objectives
Clearly defined goals that the project aims to achieve in terms of quality. These should be specific, measurable, achievable, relevant, and time-bound (SMART). Setting precise quality objectives ensures that everyone involved understands the expected standards and works towards meeting them.
Quality benchmarks should align with client specifications, industry regulations, and best practices to maintain consistency throughout the project lifecycle. Well-defined objectives also help contractors track progress and make data-driven improvements when necessary.
2. Roles and Responsibilities
A detailed outline of each team member's duties concerning quality control, ensuring accountability and clarity. Assigning responsibilities to project managers, site supervisors, and subcontractors eliminates ambiguity and ensures a smooth workflow.
When roles are clearly defined, it becomes easier to enforce quality standards, address concerns, and prevent miscommunication that could lead to costly mistakes. Ensuring that every individual understands their quality-related duties fosters teamwork and strengthens the project's overall execution.
3. Inspection and Testing Procedures
Specific methods and frequencies for inspecting work and testing materials to verify compliance with quality standards. Routine inspections at various project stages allow contractors to catch defects early and implement corrective measures before issues escalate.
Quality Control Plans should include detailed checklists for inspections, ensuring consistency in evaluations. Testing materials for durability, strength, and compliance with specifications helps avoid structural issues and enhances project reliability.
4. Documentation
Maintaining accurate records of inspections, tests, and other quality-related activities provides evidence of compliance and facilitates audits. Proper documentation supports transparency, streamlines project management, and serves as a reference in case of disputes or legal concerns.
Well-organized records also help identify recurring issues and improve future project planning. Digital documentation tools can further enhance accessibility and efficiency, making it easier to track quality-related data.
5. Corrective Actions
Procedures for addressing any deviations from quality standards, including identifying root causes and implementing solutions to prevent recurrence. A structured corrective action plan enables contractors to respond swiftly to defects, reducing downtime and avoiding additional costs.
Rather than treating quality issues as isolated incidents, a well-implemented QCP focuses on continuous improvement by analyzing patterns and making strategic adjustments. Contractors who actively refine their corrective measures build a reputation for delivering reliable, high-quality construction projects.
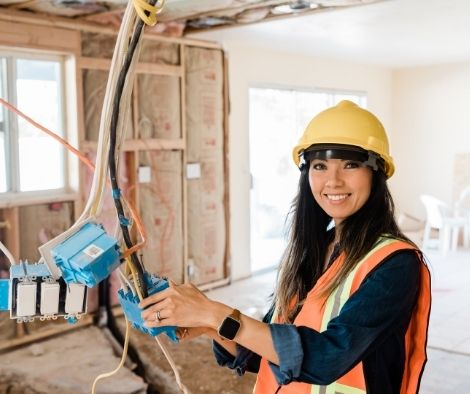
Developing a Quality Control Plan
Creating an effective Quality Control Plan (QCP) involves several steps:
1. Understand Project Specifications
Thoroughly reviewing all project documents is the first step in ensuring quality control. Contractors must analyze blueprints, engineering plans, and client requirements to gain a clear understanding of the quality benchmarks that must be met.
By identifying critical elements early, teams can align their efforts with project goals and avoid costly revisions later. Additionally, staying updated on industry codes and local regulations ensures compliance and reduces the risk of project delays.
2. Define Quality Standards
Establishing clear criteria for materials, workmanship, and construction processes is crucial for maintaining consistency. Contractors should set detailed guidelines for acceptable tolerances, finish quality, and material specifications to ensure uniformity across all project phases.
These standards should align with industry best practices and client expectations, creating a solid foundation for long-term project success. A well-defined standard prevents misinterpretations and ensures that subcontractors and suppliers deliver materials and services that meet or exceed specifications.
3. Develop Inspection and Test Plans
An effective Quality Control Plan includes well-documented inspection and testing procedures at every stage of the project. Defining when, how, and by whom inspections will be conducted ensures that potential defects are detected early. From material testing to structural inspections, a thorough plan helps maintain compliance and prevents costly rework. Utilizing checklists and digital reporting tools streamlines the inspection process, allowing for better tracking of issues and resolutions.
4. Assign Responsibilities
Assigning clear roles ensures accountability within the quality control process. Project managers, site supervisors, and field workers should understand their specific responsibilities, creating a structured approach to quality assurance. A well-organized team reduces the chances of oversight and ensures that quality standards are upheld at all times.
5. Implement Training Programs
Comprehensive training ensures that all team members are knowledgeable about the project’s quality control requirements. By educating workers on proper procedures, best practices, and safety measures, contractors can significantly reduce the risk of errors. Continuous learning opportunities help employees stay updated on new materials, techniques, and regulatory changes that affect quality control.
6. Establish Communication Protocols
Clear communication is essential for effective quality management. Contractors should implement structured reporting systems that allow team members to raise concerns, report deviations, and collaborate efficiently. Transparent communication ensures that all stakeholders—from project managers to on-site laborers—are aligned with quality expectations.
7. Monitor and Adjust
Regularly assessing the effectiveness of the Quality Control Plan is key to continuous improvement. By analyzing inspection reports, identifying recurring issues, and gathering feedback from project teams, contractors can make data-driven adjustments. This proactive approach helps enhance quality management and ensures that future projects benefit from lessons learned.
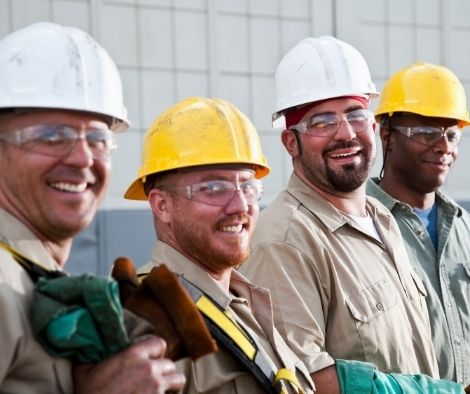
Utilize Checklists to Streamline Inspections
Incorporating detailed checklists into your inspection process can help ensure that no aspect of the project is overlooked. Checklists provide a standardized approach to inspections, making it easier to maintain consistency and quality across all project stages.
By using a structured format, contractors can systematically verify that materials, workmanship, and safety protocols meet the required standards before proceeding to the next phase.
A well-designed checklist not only enhances efficiency but also reduces the chances of missing critical details that could lead to costly errors or rework. It serves as a reference tool for site supervisors, quality control managers, and field workers, ensuring that each inspection follows a predefined set of criteria.
This structured approach minimizes subjectivity and ensures that quality control measures are applied uniformly across the entire project.
Additionally, digital checklists and mobile inspection apps allow teams to track progress in real time, log deficiencies, and instantly communicate issues that require corrective action. These tools streamline documentation, making it easier to generate reports and demonstrate compliance with project specifications and regulatory standards.
By integrating checklists into daily workflows, contractors can proactively address potential quality concerns, maintain accountability, and improve overall project outcomes.
Design Quality Control Plan
A Design Quality Control Plan focuses on ensuring that the project's design phase meets the required quality standards. This phase is critical because errors in design can lead to costly revisions, delays, or compliance issues during construction.
A well-structured plan helps prevent such setbacks by implementing systematic review and verification processes at every stage.
Design Reviews:
Regularly scheduled evaluations of design documents help identify and rectify errors early. By conducting thorough assessments, contractors and design teams can ensure that blueprints, schematics, and specifications align with project goals, construction feasibility, and industry best practices. Peer reviews and third-party assessments add another layer of validation, reducing the risk of oversight.
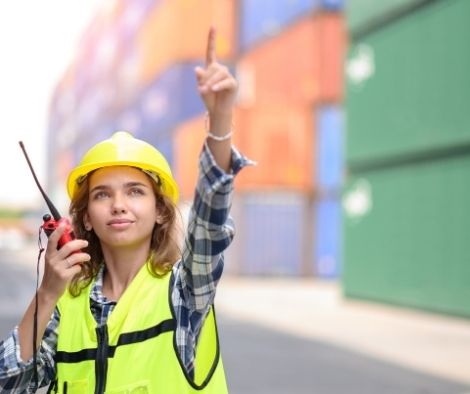
Standards Compliance:
Ensuring that designs adhere to relevant codes, regulations, and client specifications is essential for project success. This involves cross-checking designs against building codes, environmental regulations, and safety standards. Compliance measures not only prevent legal and regulatory issues but also contribute to the overall durability and efficiency of the finished structure.
Coordination:
Effective communication among architects, engineers, and stakeholders ensures that all design elements align with the project's objectives. Misalignment between teams can lead to discrepancies in execution, so collaboration tools, regular meetings, and version control systems should be in place to maintain clarity and consistency. A proactive Design Quality Control Plan minimizes risks, enhances efficiency, and sets a strong foundation for a successful build.
Implementing the Quality Control Plan
Putting the Quality Control Plan (QCP) into action requires a structured approach to ensure consistency, compliance, and continuous improvement throughout the project lifecycle. Successful implementation involves engaging all stakeholders, reinforcing accountability, and maintaining rigorous oversight of quality processes.
Kick-off Meetings:
Discussing the QCP with all stakeholders is essential for ensuring alignment and buy-in from project managers, subcontractors, and site personnel. These meetings provide an opportunity to clarify expectations, outline procedures, and address potential concerns. A well-communicated plan prevents misinterpretations that could compromise quality or lead to inefficiencies.
Regular Training:
Providing ongoing education ensures that every team member remains well-versed in current quality standards, best practices, and procedural updates. Training sessions should cover inspection protocols, material specifications, and documentation processes. Investing in workforce education minimizes errors, improves workmanship, and strengthens the project's overall quality framework.
Conclusion
Developing and implementing a Quality Control Plan isn’t just about meeting industry standards—it’s about setting your projects apart with superior craftsmanship, reliability, and efficiency. By focusing on clear objectives, well-defined roles, and meticulous inspection processes, contractors can consistently exceed client expectations and build a reputation for excellence.
Don’t leave quality to chance—take control today! Let our experts help you design a customized Quality Control Plan that streamlines your processes, minimizes risks, and ensures top-tier results on every project. Schedule a free consultation now and take the first step toward flawless execution and long-term success!