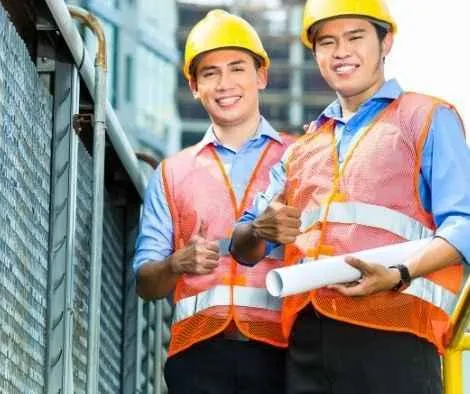
IAQ in Construction: Prioritizing Indoor Air Quality
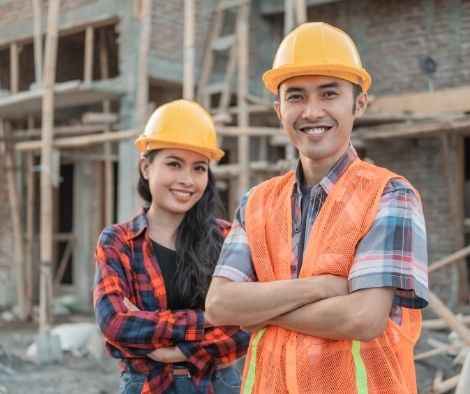
When it comes to Indoor Air Quality (IAQ) in Construction, there’s more at stake than just fresh air. Construction sites are notorious for dust, pollutants, and airborne hazards that affect both workers and the final building occupants. Poor IAQ can lead to health risks, project delays, and long-term structural issues.
A quality construction project isn’t just about durability and aesthetics—it’s about creating safe, breathable environments from the ground up. Whether it’s airborne dust from drywall installation, fumes from adhesives, or moisture buildup leading to mold, failing to address IAQ can result in costly mistakes.
The key is proactive planning, the right materials, and proven strategies that minimize hazards without disrupting workflow.
So, how can contractors, project managers, and developers prioritize IAQ on-site without compromising efficiency or budgets? The answer lies in choosing low-emission materials, implementing smart ventilation, and maintaining strict dust control throughout every phase of construction.
This guide breaks it down with practical steps, real-world strategies, and must-know best practices—so your next project isn’t just built to last, but built to breathe. Let’s get started.
Why Indoor Air Quality in Construction Matters
Health and Safety Risks
A construction site isn’t just a workspace—it’s an active environment filled with airborne hazards. From concrete dust and fiberglass particles to VOCs from paints and adhesives, exposure to these contaminants can lead to serious health risks. Workers frequently experience respiratory issues, eye irritation, and fatigue, while long-term exposure can contribute to chronic conditions like asthma and lung disease.
The best way to combat these risks is through proactive IAQ management. Implementing dust suppression techniques, high-efficiency air filtration, and proper ventilation ensures that workers aren’t constantly breathing in harmful pollutants.
A commitment to Indoor Air Quality Construction practices doesn’t just improve safety—it boosts productivity by reducing sick days and fatigue-related mistakes.
Building Performance and Longevity
Indoor air quality during construction affects far more than just worker safety—it has a lasting impact on the final building’s performance. Poor IAQ in Construction can lead to trapped moisture, mold growth, and hidden structural deterioration, all of which can compromise the integrity of the building before it’s even occupied.
Using low-emission materials, sealing off high-risk areas, and maintaining strict site cleanliness helps ensure that the finished project doesn’t just meet industry standards—it delivers a higher level of quality construction that stands the test of time.
Regulatory Compliance
Construction regulations are becoming increasingly strict, particularly when it comes to IAQ in Construction. Failing to meet OSHA, EPA, or local building codes can result in fines, project shutdowns, and legal repercussions—not to mention damage to your company’s reputation.
A well-managed IAQ strategy ensures compliance with current regulations while future-proofing your projects against even stricter environmental standards. Prioritizing Indoor Air Quality Construction isn’t just about following the rules—it’s about staying ahead of them and delivering healthier, safer, and more efficient buildings.
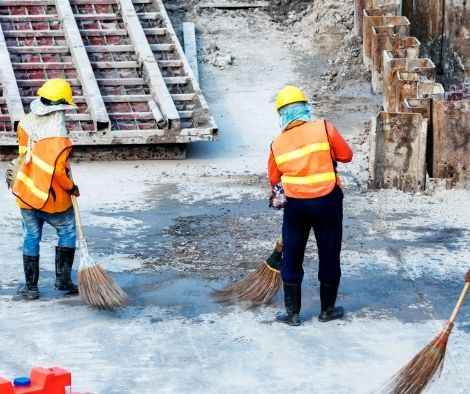
Common IAQ Challenges in Construction
Maintaining Indoor Air Quality Construction standards isn’t as simple as just keeping a site clean. Construction environments are full of airborne contaminants, fluctuating conditions, and IAQ risks that, if ignored, can jeopardize worker safety, project timelines, and the long-term health of a building.
Here are some of the most common IAQ challenges faced on construction sites—and how to address them effectively.
1. Dust and Particulate Matter
Construction activities like demolition, cutting, sanding, and grinding generate excessive amounts of dust. These fine particles, including silica dust, drywall dust, and sawdust, can linger in the air and cause serious respiratory issues for workers.
Solution:
Implementing dust suppression techniques, using high-efficiency air filters, and ensuring proper on-site ventilation can significantly reduce airborne particulates and create a safer workspace.
2. VOC Emissions from Materials
Many construction materials—paints, adhesives, sealants, and insulation—release volatile organic compounds (VOCs), which can cause headaches, nausea, and long-term respiratory problems.
Without proper ventilation, these chemicals can accumulate, creating poor IAQ in Construction projects.
Solution:
Opt for low-VOC or zero-VOC materials, ensure adequate air exchange, and store hazardous materials properly to limit exposure.
3. Mold and Moisture Buildup
Trapped moisture during construction—especially in drywall, insulation, or wood—creates the perfect breeding ground for mold. Mold growth can lead to structural damage and ongoing IAQ issues for future occupants.
Solution:
Use moisture-resistant materials, maintain humidity control on-site, and ensure proper drying and sealing of materials before closing walls or ceilings.
4. Poor Ventilation During Construction
Many construction sites operate in partially enclosed spaces where dust, fumes, and chemicals become trapped due to inadequate ventilation. Without proper air circulation, IAQ levels drop significantly, affecting both workers and long-term building health.
Solution:
Utilize temporary ventilation systems, ensure openings allow for cross-ventilation, and use air scrubbers to actively filter contaminants.
5. HVAC Contamination
If HVAC systems are installed too early, they can collect dust, debris, and pollutants before the building is even occupied. When activated, these contaminants circulate throughout the space, undermining IAQ standards in an otherwise quality construction project.
Solution:
Seal off HVAC systems during construction, perform pre-occupancy IAQ testing, and use high-efficiency filters before system activation.
By addressing these IAQ challenges early, construction teams can create safer work environments, avoid costly remediation, and deliver high-performance buildings that support health and efficiency.
Best Practices for Maintaining IAQ in Construction
Ensuring Indoor Air Quality Construction standards isn’t just about ticking boxes—it’s about protecting workers, improving building performance, and ensuring compliance. Whether you’re working on a residential project or a large commercial build, IAQ should be a top priority throughout every phase of construction.
Below are five must-follow best practices to maintain IAQ in Construction while delivering quality construction projects that support both worker safety and long-term air quality for occupants.
1. Use Low-VOC and IAQ-Friendly Materials
Many traditional construction materials contain high levels of volatile organic compounds (VOCs), which off-gas toxic chemicals into the air. Paints, adhesives, sealants, and even some flooring materials release VOCs, contributing to poor air quality and potential health issues like headaches, nausea, and respiratory irritation.
How to Reduce VOC Exposure:
Choose low-VOC or zero-VOC alternatives – These materials are widely available and help maintain safer indoor air during and after construction.
Use pre-finished materials when possible to minimize on-site chemical exposure.
Store and handle materials properly to prevent unnecessary emissions.
Schedule high-emission tasks early in the project timeline to allow for proper ventilation before occupancy.
By making thoughtful material choices, you’re not only improving IAQ in Construction but also ensuring a healthier environment for future building occupants.
2. Control Dust and Particulate Matter
Construction dust is one of the biggest threats to Indoor Air Quality Construction standards. Activities like sanding, drywall cutting, and demolition generate fine airborne particles that can linger in the air for hours or even days.
Prolonged exposure can lead to respiratory illnesses, eye irritation, and long-term lung damage.
How to Keep Dust Levels Low:
Use dust barriers like plastic sheeting or temporary walls to contain contaminated air.
Implement negative air machines to create airflow that prevents dust from spreading.
Apply water suppression techniques when cutting materials to reduce airborne dust.
Regularly clean work areas to remove settled dust before it gets stirred back into the air.
Pro Tip: Install temporary air filtration units on-site to capture dust and pollutants before they spread, keeping air quality safe and breathable for workers.
By actively managing dust, you’re creating safer conditions, reducing health risks, and preventing costly IAQ remediation later on.
3. Implement Proper Ventilation Strategies
Ventilation is critical for maintaining quality construction air standards. Without it, pollutants like VOCs, dust, and fumes become trapped, making the site hazardous. Proper ventilation ensures a constant exchange of fresh air, helping to remove contaminants and maintain air quality.
Best Ventilation Strategies for Construction Sites:
Use exhaust fans to remove fumes and airborne contaminants from enclosed areas.
Install HEPA filters in air systems to capture small airborne particles.
Increase natural ventilation by keeping doors and windows open whenever possible.
Utilize air scrubbers for high-risk zones where dust or chemical exposure is unavoidable.
Proper ventilation doesn’t just protect workers—it also ensures the final building is free of trapped contaminants, preventing long-term IAQ issues for occupants.
4. Prevent Moisture Issues to Avoid Mold Growth
Moisture is one of the biggest threats to IAQ in Construction. If not controlled, it can lead to mold growth, material degradation, and hidden structural damage. Mold spores travel through the air and can cause serious respiratory issues, particularly for those with allergies or asthma.
How to Prevent Moisture-Related IAQ Issues:
Use dehumidifiers in humid conditions to keep moisture levels low.
Properly seal roofing, windows, and exterior walls to prevent water intrusion.
Install moisture-resistant drywall in high-risk areas like bathrooms, kitchens, and basements.
Ensure proper drainage around the site to divert water away from structures.
Preventing moisture issues ensures a healthier worksite, better Indoor Air Quality Construction, and a structurally sound building that won’t develop hidden IAQ problems over time.
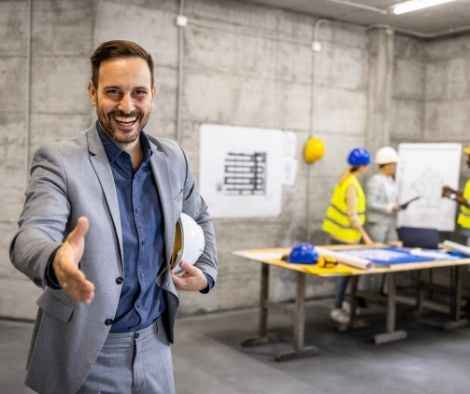
5. Train Workers on IAQ Best Practices
A well-trained team is one of the most powerful tools in ensuring IAQ in Construction remains a priority. Every worker on-site contributes to air quality, whether through material handling, work habits, or equipment use.
Educating teams on IAQ best practices creates a culture of awareness, responsibility, and compliance.
Key IAQ Training Areas:
Proper material handling to minimize emissions from high-VOC substances.
Using PPE correctly (e.g., respirators and masks) to prevent inhaling dust and fumes.
Recognizing IAQ hazards early to prevent small issues from becoming major problems.
Following site ventilation plans to ensure air quality remains at safe levels.
When workers understand how their actions impact IAQ, they’re more likely to take proactive steps to maintain a clean and safe environment—resulting in better air quality, fewer health risks, and stronger overall project outcomes.
By implementing these IAQ best practices, construction teams can reduce exposure to pollutants, improve worker safety, and deliver healthier buildings.
Prioritizing Indoor Air Quality Construction isn’t just about meeting regulations—it’s about building smarter, safer, and cleaner environments for the future.
How to Improve IAQ in Different Construction Phases
Pre-Construction Planning
Choose IAQ-friendly materials
Develop an air quality management plan
Schedule inspections for potential pollutants
During Construction
Use proper containment measures for dust and debris
Maintain ventilation systems and air filters
Monitor IAQ levels with air quality sensors
Post-Construction & Occupancy
Flush out pollutants before occupancy.
Conduct IAQ testing.
Ensure proper HVAC setup for long-term air quality
Regulatory Guidelines for IAQ in Construction
In the world of Indoor Air Quality Construction, adhering to regulatory standards is essential not just for compliance but for ensuring the long-term health and safety of workers and future building occupants.
By following established guidelines, contractors can improve IAQ in Construction while ensuring that their projects meet both legal and industry standards.
Key Regulatory Bodies to Know:
OSHA (Occupational Safety and Health Administration):
OSHA regulates worker exposure to airborne contaminants and sets exposure limits for dust, fumes, and vapors on construction sites. By maintaining safe air quality standards, contractors ensure the protection of workers' health during and after construction. Regular air quality monitoring and PPE usage help in staying compliant with OSHA’s standards, promoting a safe, healthy workplace.
EPA (Environmental Protection Agency):
The EPA provides guidelines for sustainable construction practices, focusing on how to minimize pollutants during building projects. Their IAQ guidelines cover everything from proper ventilation to managing toxic substances. By incorporating these recommendations into your building strategy, you contribute to a higher standard of quality construction that prioritizes environmental sustainability.
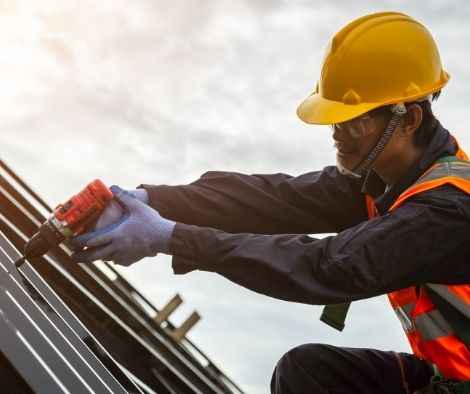
ASHRAE (American Society of Heating, Refrigerating and Air-Conditioning Engineers):
ASHRAE offers specific HVAC system recommendations to control IAQ by providing better airflow, filtration, and humidity control. Following these recommendations ensures that the air within your building remains clean and safe, ensuring long-term indoor air quality for all occupants.
Adhering to these regulatory guidelines not only supports compliance but ensures that IAQ in Construction remains a cornerstone of your commitment to quality construction. With a strong focus on health, safety, and sustainability, following these best practices allows for more effective, compliant, and healthier construction projects.
Breathe Easy, Build Better
Indoor Air Quality in Construction is not just a regulatory checkbox—it’s a fundamental aspect of safety, efficiency, and long-term building health. By implementing proper IAQ strategies, construction teams can create healthier environments for workers and future occupants alike.
Ready to Build Smarter, Safer, and Cleaner?
IAQ isn’t just about meeting standards—it’s about protecting your team, delivering quality construction, and future-proofing your projects. Don’t let poor air quality slow you down.
Take action today—review your IAQ strategy, upgrade your materials, and ensure your site is a place where safety and performance go hand in hand.
Need expert guidance on improving IAQ for your next project? Let’s make it happen—reach out now and build with confidence.