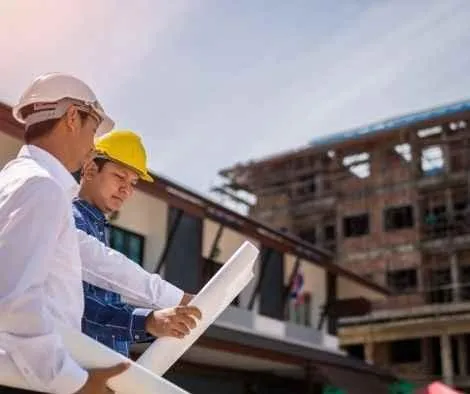
Key Elements of Quality Control Plans
In the construction industry, quality control is a cornerstone of successful project execution. From ensuring compliance with safety standards to delivering structures that stand the test of time, quality control in construction is essential. A well-defined quality management plan not only guarantees high standards but also fosters client trust and enhances project efficiency.
In this blog, we delve into the key elements of quality control plans, shedding light on how they ensure quality assurance in construction while maintaining industry best practices.
Quality control in construction encompasses a systematic approach to identifying, addressing, and mitigating potential issues before they escalate. It involves a combination of preventive measures, real-time monitoring, and corrective actions to ensure that every phase of the project aligns with predetermined quality benchmarks. Without an effective quality management plan, construction projects risk delays, increased costs, and diminished client satisfaction.
Moreover, quality assurance in construction goes hand-in-hand with quality control. While the latter focuses on inspecting and verifying the output, quality assurance emphasizes setting up processes to prevent defects from occurring in the first place. This dual approach ensures that both the processes and the final deliverables meet industry standards and client expectations.
A strong quality control plan also plays a pivotal role in fostering a culture of accountability among team members. When roles and responsibilities are clearly defined, every stakeholder is aware of their contribution to maintaining quality standards. This not only streamlines operations but also reduces the likelihood of errors and miscommunication.
In today’s competitive landscape, adopting advanced technologies like Building Information Modeling (BIM) and construction management software has further enhanced quality control practices. These tools enable real-time tracking, data analysis, and seamless collaboration, making it easier to identify and address potential issues promptly. Incorporating these technologies into your quality management plan can significantly improve project outcomes.
Additionally, continuous training and development of the workforce are crucial components of quality control in construction. A well-trained team is better equipped to handle challenges, adhere to standards, and implement best practices effectively. Investing in training programs not only boosts morale but also enhances the overall quality of work.
The importance of stakeholder engagement in quality management cannot be overstated. Regular communication and collaboration with clients, contractors, and suppliers ensure that everyone is aligned on quality expectations and project goals. This collaborative approach minimizes conflicts and fosters a sense of shared responsibility for the project’s success.
Why Quality Control Plans Are Vital in Construction
Ensuring Safety and Compliance
Safety is paramount in construction projects. A robust quality control plan ensures that all safety protocols are adhered to, minimizing risks for workers and end-users. Moreover, compliance with industry standards and government regulations is critical to avoid legal and financial repercussions.
Implementing safety measures also involves continuous monitoring of on-site activities. Regular safety audits, hazard assessments, and emergency response drills can significantly reduce accidents and enhance overall safety performance. Ensuring proper use of personal protective equipment (PPE) and enforcing strict safety guidelines further bolster safety standards.
Enhancing Project Efficiency
Quality control in construction helps identify potential issues early, saving time and resources. Addressing these problems proactively ensures smoother workflows and minimizes project delays. Efficient workflows not only improve productivity but also optimize resource allocation, reducing wastage and controlling costs.
Moreover, a structured quality management plan streamlines communication among project stakeholders. Clear reporting procedures and real-time updates help in resolving issues promptly, avoiding unnecessary bottlenecks. By maintaining a focus on quality, projects can achieve better timelines and superior results.
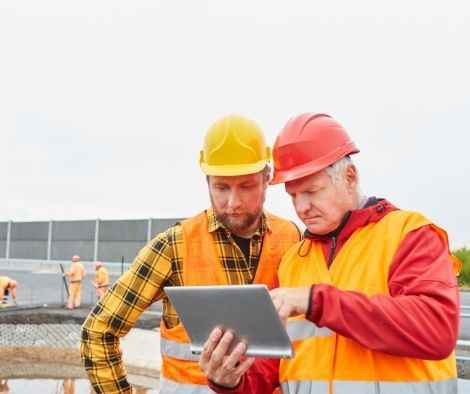
Building Client Confidence
Clients expect reliable and durable structures. A well-executed quality management plan demonstrates professionalism and commitment to delivering superior results, fostering long-term relationships. Transparent quality assurance practices also instill confidence, as clients can see tangible evidence of the project’s adherence to high standards.
Engaging clients in the quality control process can further strengthen trust. Regular updates, milestone reviews, and open communication ensure that clients are well-informed and reassured about project progress. This proactive approach not only enhances client satisfaction but also paves the way for repeat business and positive referrals.
Furthermore, a focus on quality leads to higher client satisfaction ratings, which can enhance the company's reputation in the market. Happy clients are more likely to recommend your services to others, creating valuable word-of-mouth marketing opportunities.
By exceeding client expectations, construction firms can also position themselves as industry leaders. Demonstrating consistent quality in completed projects becomes a testament to the company’s expertise and reliability, attracting more high-profile projects.
In addition to these benefits, a robust quality control plan contributes to cost efficiency. Early detection of defects prevents costly rework, helping to maintain the project’s budget. This not only ensures financial stability but also reduces stress for project managers and stakeholders.
Key Elements of a Quality Control Plan
Clear Objectives and Standards
Every quality control plan begins with defining clear objectives. What does "quality" mean for the project? Establishing benchmarks and standards ensures that everyone involved has a shared understanding of expectations.
Example: Setting concrete strength standards or specifying acceptable tolerances for material dimensions.
Develop measurable quality goals to align with client requirements.
Communicate these standards to all team members effectively.
Use industry best practices and regulatory guidelines to frame objectives.
Periodically review objectives to ensure they remain relevant.
Incorporate lessons learned from previous projects into quality benchmarks.
Detailed Scope of Work
A quality management plan should include a detailed scope of work. This defines the tasks, responsibilities, and timelines to ensure accountability at every stage.
Tip: Break down the project into phases, each with specific quality benchmarks.
Outline specific deliverables for each phase of the project.
Identify potential risks and include mitigation strategies.
Allocate resources efficiently to meet quality expectations.
Define quality metrics for evaluating project progress.
Engage all stakeholders in the development of the scope of work.
Material and Equipment Specifications
High-quality materials and equipment are foundational to construction quality assurance. The plan must specify approved suppliers and materials, along with testing protocols to verify compliance.
Example: Testing cement for consistency or ensuring steel meets tensile strength requirements.
Create a list of pre-approved suppliers and vendors.
Conduct periodic audits of material quality during procurement.
Specify acceptable ranges for material properties and tolerances.
Include contingency plans for material shortages or delays.
Maintain comprehensive records of material certifications and test results.
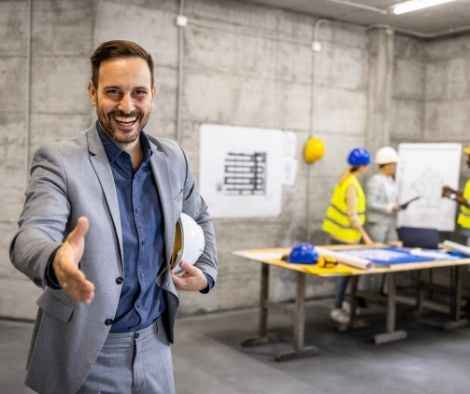
Inspection and Testing Procedures
Regular inspections and rigorous testing are crucial components of quality control. These procedures should be documented in the plan, along with criteria for acceptance or rejection.
Tip: Incorporate third-party inspections for unbiased assessments.
Schedule inspections at critical milestones of the project.
Develop a checklist for each type of inspection to ensure thoroughness.
Use modern tools like drones or sensors for enhanced testing accuracy.
Train staff on inspection procedures to minimize human errors.
Establish a clear process for addressing non-conformities identified during inspections.
Roles and Responsibilities
Assigning roles is critical for accountability. The quality control manager, site supervisors, and workers must clearly understand their responsibilities.
Key Roles: Quality control manager, safety officer, and inspection personnel.
Define roles and responsibilities in writing to avoid ambiguity.
Ensure that all team members understand their specific quality-related duties.
Provide training and resources to help team members fulfill their roles effectively.
Assign backup personnel for key roles to ensure continuity.
Include subcontractors and suppliers in the quality control framework.
Document Control and Reporting
A good quality control plan includes robust documentation practices. Maintaining detailed records ensures traceability and accountability.
Example: Daily progress reports, material testing logs, and inspection reports.
Use digital tools to streamline documentation and reporting processes.
Maintain a centralized repository for all project documents.
Regularly update records to reflect the latest project developments.
Establish access controls to protect sensitive information.
Use documented insights to inform future project planning and quality improvements.
Continuous Improvement Mechanisms
Construction projects often encounter unforeseen challenges. Quality management plans should include mechanisms for continuous improvement, such as feedback loops and regular audits.
Tip: Conduct post-project reviews to refine processes for future projects.
Implement a structured process for collecting and analyzing feedback.
Use audit findings to identify gaps in quality control practices.
Encourage team members to propose innovative solutions to recurring issues.
Regularly update quality standards to align with industry advancements.
Create a culture of continuous learning to enhance overall project quality.
Implementing Quality Control Plans: Best Practices
Incorporate Technology
Leverage technology like construction management software to streamline inspections, track defects, and ensure compliance with quality standards. Examples: Drones for site inspections, BIM (Building Information Modeling) for design validation. By adopting innovative tools, you ensure a more efficient approach to quality control in construction and maintain higher levels of accuracy.
Train Your Team
Invest in training programs to ensure all team members understand quality control procedures and their role in maintaining standards. This knowledge empowers the workforce to spot potential issues early, minimizing costly rework and ensuring the integrity of your Quality Management Plan.
Engage Stakeholders
Collaboration with all stakeholders—from clients to subcontractors—ensures alignment on quality expectations and fosters accountability. When everyone is on the same page, it becomes easier to implement Quality Assurance in Construction and mitigate risks.
Monitor Performance Metrics
Regularly review performance metrics to identify trends and areas for improvement. Use KPIs (Key Performance Indicators) such as defect rates and inspection pass percentages to assess whether your quality control plan is being effectively implemented.
Conduct Regular Audits
Implement periodic internal audits to assess the effectiveness of your Quality Management Plan. This will help identify any gaps in your processes, allowing for quick corrective actions before problems escalate.
Implement Standardized Procedures
Establish and document standardized procedures for inspections, testing, and reporting. This ensures consistency and reliability across all stages of construction and allows you to maintain effective quality control in construction throughout the project lifecycle.
Use Checklists for Inspections
Develop detailed inspection checklists for various project stages. These checklists serve as guides to ensure all critical aspects of the project are inspected for quality, helping you stay on track and meet the Quality Assurance in Construction standards.
Ensure Effective Communication
Maintain open lines of communication with all parties involved in the project. Clear communication is essential for understanding quality control in construction standards and addressing potential issues quickly.
Promote Continuous Improvement
Encourage a culture of continuous improvement by gathering feedback from team members and stakeholders. Review lessons learned from previous projects and apply them to future construction efforts to enhance your Quality Management Plan.
Establish Clear Roles and Responsibilities
Define and assign clear roles and responsibilities to all team members for ensuring quality throughout the project. This minimizes confusion and ensures everyone is held accountable for their part in meeting quality control in construction standards.
Track Defects and Corrective Actions
Develop a system for tracking defects, non-conformance, and the corrective actions taken. This documentation can serve as a valuable reference for future projects and ensure Quality Assurance in Construction is consistently applied.
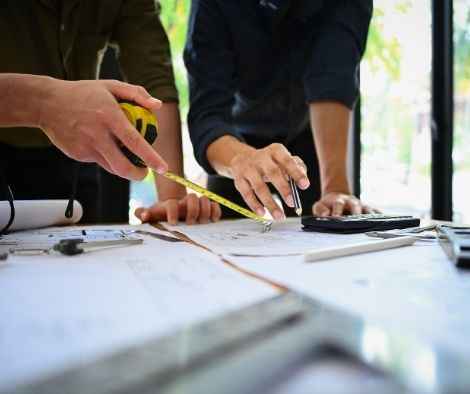
Develop a Risk Management Strategy
Identify potential risks that could impact the quality of the project and develop a strategy for managing those risks. This proactive approach helps you address problems before they affect the overall quality of the construction.
Conduct Pre-Construction Meetings
Hold pre-construction meetings to review quality standards with all involved parties. These meetings can align expectations and ensure that everyone understands their role in implementing the Quality Management Plan.
Utilize Real-Time Data
Leverage real-time data to track project progress and identify any emerging quality issues. Using up-to-date information helps you make timely decisions and ensures the quality control in the construction plan remains on track.
Incorporate Sustainability Standards
Incorporate sustainability and environmental standards into your quality control plan. These standards ensure the project meets regulatory requirements and aligns with best practices for environmentally responsible construction, enhancing the overall quality and compliance with Quality Assurance in Construction principles.
Overcoming Common Challenges
Resistance to Change
Some team members may resist new quality control procedures. Address this by demonstrating the benefits and providing adequate training. Clearly communicate how implementing a Quality Management Plan ensures better long-term results, making the adoption of Quality Control in Construction smoother and more effective.
Budget Constraints
Quality control can be perceived as an added expense. Highlight the long-term cost savings through reduced rework and enhanced client satisfaction. When teams understand the return on investment in Quality Assurance in Construction, they’ll be more willing to allocate resources to this crucial aspect.
Communication Gaps
Miscommunication can derail quality initiatives. Ensure clear and consistent communication channels among all team members. Establishing these channels is vital to successfully managing Quality Control in Construction, ensuring that everyone is aligned with the Key Elements of Quality Control Plans.
Lack of Proper Documentation
Without proper documentation of quality control measures, tracking issues can be challenging. Ensure all inspections, tests, and corrective actions are documented clearly in line with your Quality Management Plan to facilitate future audits and improvements.
Inconsistent Implementation
To avoid gaps in quality control execution, ensure the application of procedures is consistent across the project. A robust Quality Assurance in Construction strategy will help standardize practices and maintain high-quality outputs at every stage.
Training Gaps
Ensure that every team member is adequately trained in Quality Control in Construction practices. Continuous learning opportunities will help improve skills and enhance overall project quality, reducing errors and maintaining high standards in line with your Quality Management Plan.
Conclusion
Quality control plans are indispensable for the successful execution of construction projects. By focusing on clear objectives, robust procedures, and continuous improvement, these plans ensure that projects meet high standards while fostering efficiency and client satisfaction. Quality assurance in construction complements quality control by preventing issues at the outset, creating a comprehensive approach to project excellence.
Investing in a well-structured quality management plan is not just a best practice; it’s a necessity in today’s competitive construction landscape. Implement these key elements to elevate your projects and build lasting success.