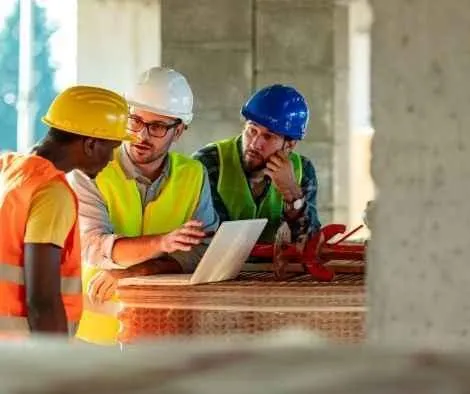
OSHA Compliance: Key Steps for Safety and Accident Prevention
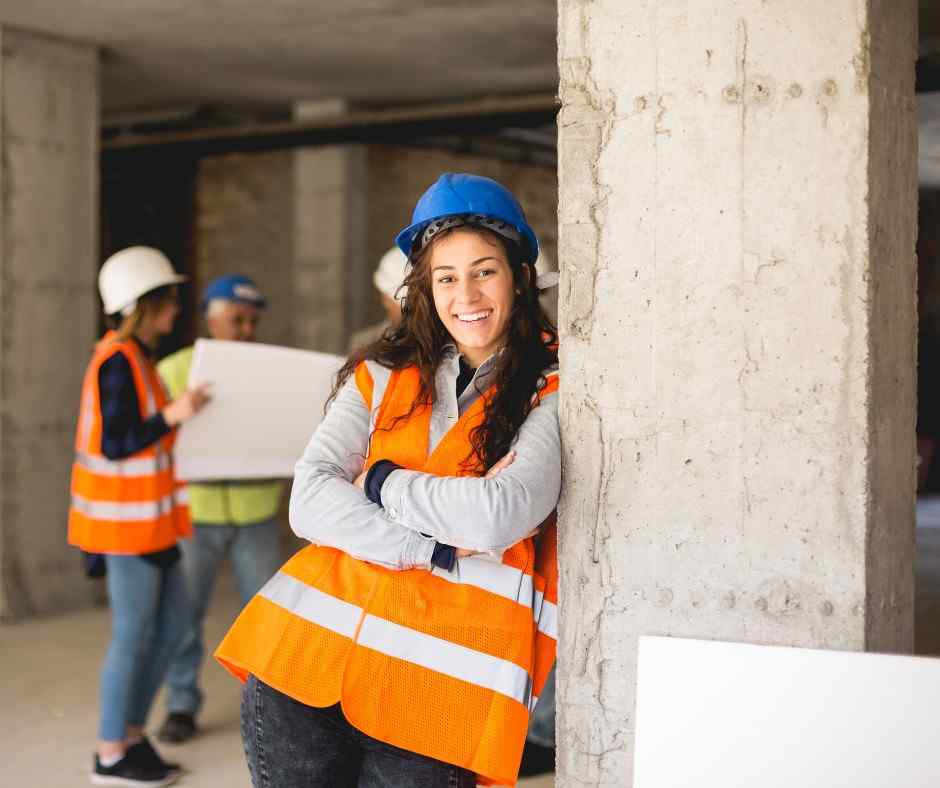
Workplace safety is a cornerstone of organizational success, and OSHA compliance ensures that all employees work in a protected environment. Beyond being a legal requirement, OSHA compliance fosters a proactive approach to identifying and mitigating risks before they escalate.
It involves periodic workplace inspections, systematic employee training, and the establishment of a culture where safety is prioritized at every level. Employers must focus on continuous improvement by using tools like hazard analysis, safety audits, and emergency response plans. These efforts not only safeguard employees but also reduce operational disruptions and enhance overall productivity.
What is OSHA Compliance?
The Occupational Safety and Health Administration (OSHA) ensures safe and healthful working environments through federal regulations. Achieving OSHA compliance involves recognizing workplace hazards, implementing safety measures, and educating employees on best practices to maintain safety standards.
Why OSHA Compliance Matters
Prevents Workplace Accidents
By reducing injuries and accidents, OSHA compliance ensures employees' well-being and creates a more secure environment. This helps retain staff and avoid operational disruptions caused by preventable incidents.Lowers Legal Risks
Non-compliance can lead to steep penalties, lawsuits, and reputational damage. By adhering to OSHA standards, businesses mitigate these risks, fostering a sense of trust with employees and stakeholders.Improves Productivity
A safe workplace enables employees to focus on their tasks without fear of injury. When employees feel secure, morale improves, and the overall workflow becomes more efficient.Builds a Culture of Safety
OSHA compliance promotes a proactive approach to safety, encouraging employees to recognize hazards and take part in creating safer workplaces. This mindset reduces complacency and strengthens teamwork.Financial Savings
Workplace accidents often result in medical expenses, worker compensation claims, and increased insurance premiums. Complying with OSHA guidelines minimizes these costs by reducing preventable incidents.
Components of OSHA Compliance
Hazard Identification and Assessment: Regular inspections to identify potential risks.
Training Programs: Educating employees on safety protocols, equipment handling, and emergency response procedures.
Recordkeeping and Reporting: Maintaining detailed records of injuries, illnesses, and safety measures to remain accountable.
Emergency Preparedness: Ensuring facilities have proper evacuation plans, fire safety protocols, and first aid resources.
OSHA compliance is not merely about avoiding fines; it’s a commitment to safeguarding lives and creating a culture of care and responsibility in the workplace.
Key Elements of OSHA Compliance
1. Hazard Identification and Assessment
Conduct regular inspections to detect workplace hazards, such as chemical spills, electrical issues, or machinery malfunctions.
Evaluate slip, trip, and fall risks using tools like safety audits, incident reports, and observation checklists.
Implement technology like wearable safety devices and monitoring systems to identify potential risks in real time.
2. Development of a Safety Management System (SMS)
Create emergency response plans tailored to the organization’s specific risks, including evacuation procedures and medical response protocols.
Schedule preventive maintenance to ensure that machinery and equipment are functioning optimally.
Establish clear reporting systems, encouraging employees to report potential risks without fear of retaliation. Use digital platforms for seamless issue tracking.
3. Employee Training
Design interactive workshops and simulations for employees to recognize hazards, understand OSHA standards, and use safety equipment.
Offer comprehensive training for specialized roles, such as handling hazardous materials or operating heavy machinery.
Develop refresher courses to keep employees updated on new safety regulations, tools, and protocols.
Integrate e-learning platforms to deliver training sessions that are accessible anytime.
Additional Considerations
Documentation and Recordkeeping: Maintain accurate logs of inspections, injuries, and corrective actions. Ensure compliance with OSHA’s reporting requirements.
Personal Protective Equipment (PPE): Supply and mandate the use of OSHA-approved gear, such as helmets, gloves, and safety glasses. Conduct regular inspections to verify equipment suitability.
Emergency Preparedness Drills: Conduct periodic mock drills to test the effectiveness of the emergency plans and enhance employees’ readiness.
Safety Committees: Form committees that include employees and management to regularly review safety practices and propose improvements.
Continuous Improvement: Use feedback from audits and employee input to refine safety measures and stay updated with OSHA guidelines.
By addressing these elements comprehensively, organizations can ensure a safer workplace and full compliance with OSHA regulations.
OSHA Standards for Different Industries
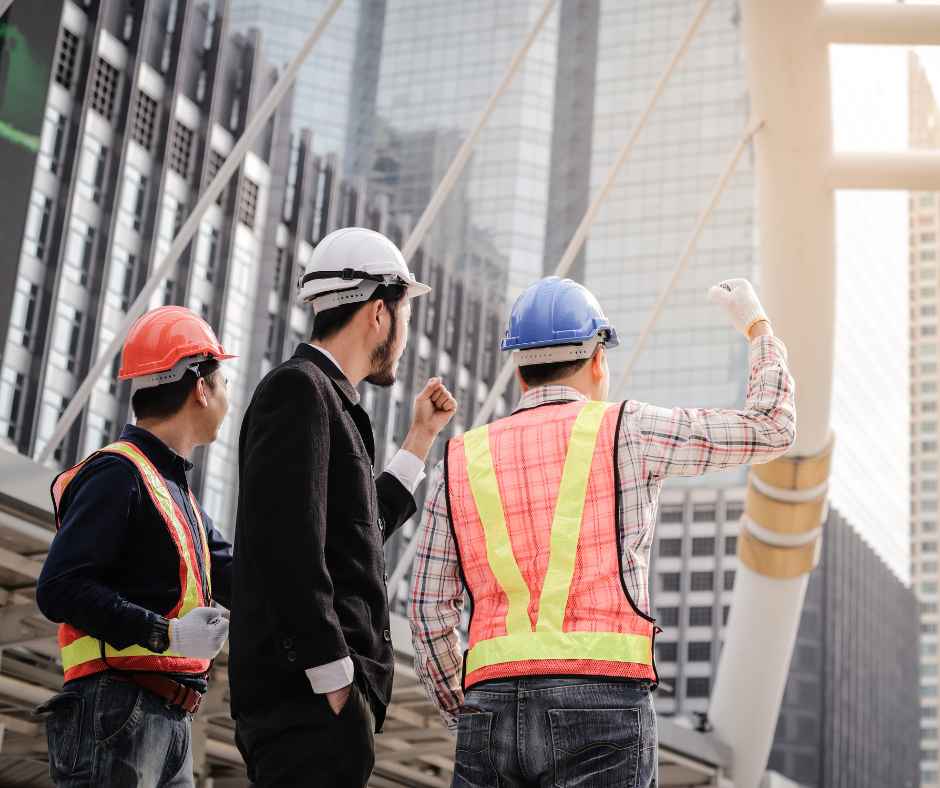
Construction
The construction industry faces unique hazards that OSHA standards aim to address:
Scaffolding Safety Requirements: Employers must ensure proper installation, use, and maintenance of scaffolds to prevent falls. Scaffold platforms should support at least four times the intended load.
Fall Protection Systems: OSHA mandates fall protection measures such as guardrails, harnesses, and safety nets for workers at heights of six feet or more. Employers must train workers on proper equipment use.
Excavation and Trenching: Protective systems are required for trenching operations to prevent cave-ins, such as benching, shoring, or sloping.
Manufacturing
Manufacturing environments involve machinery and repetitive tasks, leading to specific OSHA guidelines.
Machine Guarding Regulations: Equipment like presses, saws, and conveyors must have guards to protect workers from moving parts. Inspections ensure compliance with ANSI standards.
Noise Exposure Limits: OSHA’s permissible exposure limit (PEL) is 90 decibels over an 8-hour workday. Hearing protection programs must be provided to employees exposed to higher levels.
Lockout/Tagout Procedures: OSHA requires strict energy control protocols during maintenance to prevent accidental machinery start-ups.
Healthcare
Healthcare facilities present biological and ergonomic hazards that OSHA addresses:
Bloodborne Pathogen Controls: Employers must implement an exposure control plan, including PPE, needle safety, and hepatitis B vaccinations for at-risk workers.
Safe Patient Handling Techniques: OSHA encourages the use of mechanical lifts, transfer aids, and ergonomic training to reduce musculoskeletal injuries.
Infection Control Measures: Standards require proper disposal of sharps, adequate ventilation, and training on personal hygiene practices to limit exposure to infectious diseases.
Additional Industry-Specific OSHA Guidelines
Retail: Guidelines for avoiding ergonomic injuries, such as those from repetitive stocking tasks or heavy lifting.
Agriculture: Standards for pesticide use, grain handling safety, and protective measures against respiratory hazards.
Oil and Gas: Regulations for confined space entry, blowout prevention systems, and handling hazardous chemicals.
Understanding these industry-specific OSHA standards ensures tailored safety measures, reducing workplace hazards and improving compliance.
Steps for Ensuring OSHA Compliance
1. Conduct Regular Inspections
Workplace inspections are essential for identifying hazards and maintaining OSHA compliance:
Frequency: Perform daily, weekly, or monthly inspections based on workplace complexity.
Tools: Use OSHA inspection checklists tailored to your industry to ensure thorough evaluations.
Third-Party Audits: External safety consultants can provide impartial assessments and improvement suggestions.
2. Establish Written Policies
A comprehensive safety manual provides a clear framework for compliance:
Contents: Include emergency evacuation plans, hazard communication protocols, and equipment usage guidelines.
Accessibility: Store policies in a centralized location (digital or physical) and provide multilingual versions if needed.
Periodic Updates: Regularly revise policies to align with changing OSHA regulations and workplace conditions.
3. Maintain Accurate Records
Detailed recordkeeping is critical for compliance and accountability:
OSHA 300 Logs: Document all workplace injuries and illnesses to analyze patterns and reduce risks.
Training Records: Maintain logs of employee training sessions, including dates, topics, and participant lists.
Inspection Records: Record equipment inspections, corrective actions, and maintenance schedules to demonstrate compliance.
4. Provide Proper Equipment
Ensuring employees have the right tools and PPE minimizes workplace hazards:
Types of PPE: Supply gloves, helmets, goggles, and specialized gear (e.g., fall protection harnesses) based on job requirements.
Fit and Comfort: Regularly check that PPE fits properly and is comfortable to encourage consistent use.
Maintenance: Inspect and replace damaged or worn equipment to uphold safety standards.
5. Foster a Culture of Safety
A proactive safety culture helps sustain long-term compliance:
Open Communication: Create an environment where employees feel comfortable reporting hazards without fear of retaliation.
Incentives: Recognize and reward employees who actively promote safety practices.
Leadership Involvement: Encourage managers to model safe behavior and participate in safety initiatives.
6. Conduct Ongoing Employee Training
Education ensures that workers understand their roles in maintaining safety:
Initial Onboarding: Provide comprehensive training for new hires on company-specific safety policies.
Refresher Courses: Offer periodic training sessions to keep employees updated on new OSHA standards.
Specialized Training: Conduct focused programs for high-risk roles, such as equipment operators and chemical handlers.
7. Implement Hazard Communication Standards (HCS)
Clear communication prevents misunderstandings about workplace risks:
Labeling: Use OSHA-compliant labels and safety data sheets (SDS) for all hazardous materials.
Training: Ensure employees know how to read labels and SDS documents to understand potential risks.
Emergency Procedures: Develop and communicate action plans for responding to chemical spills or other emergencies.
8. Conduct Emergency Drills
Simulating emergency situations prepares employees for real-world crises:
Types of Drills: Plan for scenarios like fires, chemical leaks, and natural disasters.
Frequency: Schedule drills annually or semi-annually, depending on workplace risk levels.
Feedback: Debrief after drills to identify areas for improvement and update protocols accordingly.
Preventing Workplace Accidents
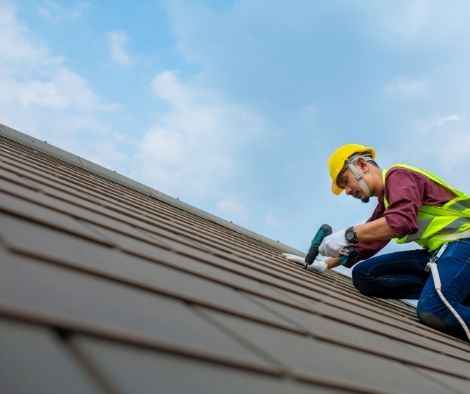
A. Fall Prevention
Falls are one of the most common and costly workplace accidents. Implement the following strategies:
Install Guardrails: Place sturdy guardrails around elevated work areas, including stairwells and rooftops.
Inspect Equipment Regularly: Conduct routine checks on ladders, scaffolds, and fall protection systems for damage or wear.
Provide Fall Arrest Systems: Supply harnesses and lifelines for employees working at heights and train them on proper use.
Keep Walkways Clear: Ensure that floors are free of obstructions, spills, or uneven surfaces that can cause trips.
B. Ergonomics
Ergonomic issues can lead to chronic injuries and reduced productivity. Address these problems by:
Adjustable Workstations: Provide desks and chairs that can be customized to support proper posture.
Anti-Fatigue Mats: Use these for employees who stand for long periods to reduce strain on legs and back.
Proper Lifting Techniques: Train employees on how to lift heavy objects safely, emphasizing the use of legs instead of the back.
Break Schedules: Encourage workers to take short breaks to stretch and reset their posture during long shifts.
C. Machine Safety
Machinery-related accidents can cause severe injuries but are largely preventable with proper safety measures:
Guarding Mechanisms: Install physical barriers like blade guards or interlocks to prevent accidental contact.
Lockout/Tagout Procedures: Implement these procedures to ensure machines are turned off and de-energized during maintenance.
Operator Training: Train workers to use equipment properly and understand emergency shutdown procedures.
Preventive Maintenance: Regularly inspect and maintain machinery to avoid unexpected failures that could lead to accidents.
D. Emergency Preparedness
Proper preparation can save lives in critical situations:
Fire Safety Plans: Equip workplaces with fire extinguishers and smoke detectors, and clearly mark all emergency exits.
Evacuation Drills: Conduct practice drills for scenarios like fires, chemical spills, and severe weather events to ensure employees know the protocols.
First-Aid Training: Train select employees in first-aid response, including CPR, to handle injuries before professional help arrives.
Emergency Supplies: Maintain stocked first-aid kits, fire blankets, and emergency lighting in accessible areas.
By addressing these key areas, employers can significantly reduce the likelihood of workplace accidents while creating a safer and more efficient environment.
Role of Technology in OSHA Compliance
Technology plays a pivotal role in making OSHA compliance more efficient and effective. Here’s how:
1. Safety Management Software
Centralized Tracking: Digital tools help track safety inspections, incident reporting, and employee training schedules in one place.
Real-Time Alerts: These platforms can notify managers of potential compliance risks or overdue tasks, enabling swift corrective actions.
Reporting and Analytics: Generate compliance reports to identify trends and improve safety measures.
2. IoT Sensors
Environmental Monitoring: Devices can measure air quality, humidity, noise levels, and temperature, ensuring workplaces remain within OSHA-regulated limits.
Hazard Detection: Sensors can detect gas leaks or structural vibrations and alert workers to evacuate immediately.
Worker Wearables: Smart helmets and wristbands track fatigue, heart rate, and location, reducing risks for employees in hazardous areas.
3. Virtual Reality (VR) Training
Immersive Learning: VR enables workers to practice high-risk scenarios, like operating machinery or handling hazardous materials, in safe, controlled environments.
Engaging Training: Employees retain more knowledge through interactive simulations compared to traditional methods.
Scenario Customization: Tailor simulations to industry-specific risks, ensuring workers are prepared for real-world challenges.
By leveraging these tools, businesses can enhance workplace safety while simplifying OSHA compliance.
Common OSHA Violations to Avoid
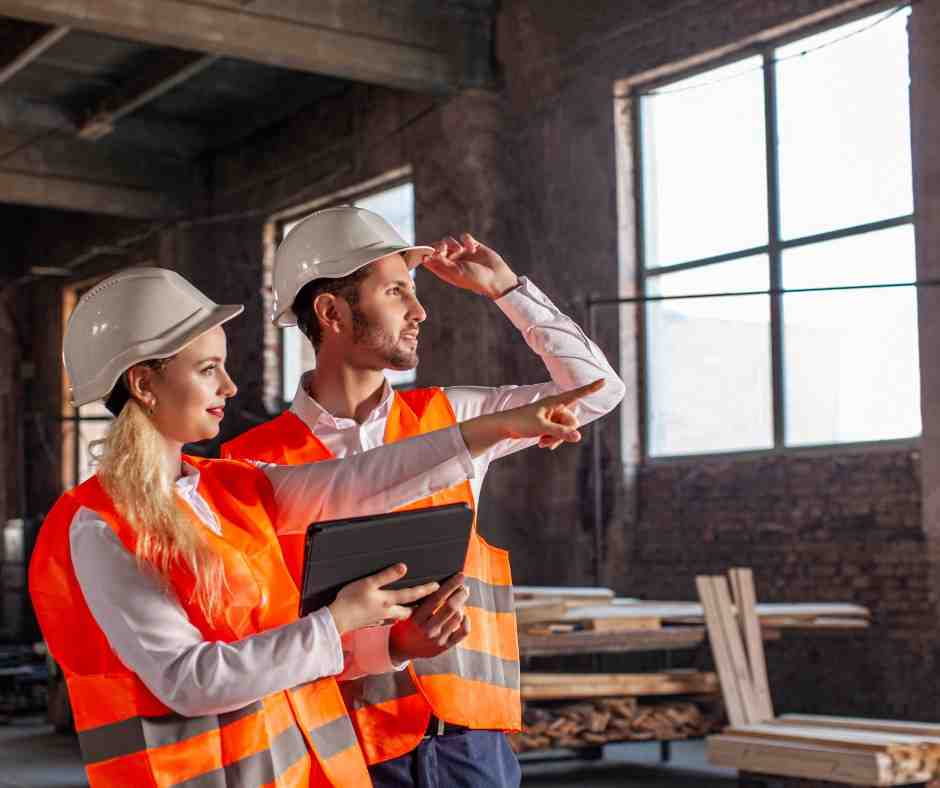
Avoiding common OSHA violations is essential for maintaining a safe workplace and avoiding penalties. Some frequently cited violations include:
1. Lack of Fall Protection
Ensure guardrails, safety harnesses, and fall arrest systems are in place for elevated work areas.
Conduct regular inspections of ladders, scaffolds, and walkways to identify hazards.
2. Inadequate Hazard Communication
Provide proper labeling for hazardous substances.
Train employees to understand Safety Data Sheets (SDS) and chemical handling procedures.
3. Improper Machine Guarding
Install adequate guarding on machines to prevent contact with moving parts.
Regularly check and maintain safety mechanisms.
4. Electrical Safety Violations
Use proper lockout/tagout (LOTO) procedures to de-energize equipment before maintenance.
Ensure all electrical panels are accessible and clearly labeled.
5. Insufficient PPE
Provide employees with properly fitting personal protective equipment (PPE).
Train them on correct usage and ensure regular replacement of worn-out gear.
Benefits of OSHA Compliance
Adhering to OSHA standards goes beyond avoiding penalties and creates long-term advantages for businesses:
Increased Employee Morale: A safe workplace demonstrates care for employee well-being, boosting job satisfaction.
Better Employee Retention: Workers are more likely to stay in environments prioritizing safety.
Improved Insurance Rates: A good safety record often leads to lower workers’ compensation premiums.
Higher Productivity: Employees perform better in environments free from hazards and disruptions.
Legal Protection: Comprehensive compliance reduces liability in case of workplace incidents.
Conclusion: Prioritize Safety and Accident Prevention
Achieving OSHA compliance is more than a legal obligation—it’s a commitment to the safety and well-being of your workforce. By following these steps, businesses can create a secure environment, prevent accidents, and thrive in a competitive marketplace.
Whether you're a construction firm or a small business, investing in safety measures and fostering a culture of prevention will lead to sustainable success. Stay proactive, implement best practices, and ensure that your organization is always ready to meet OSHA standards.