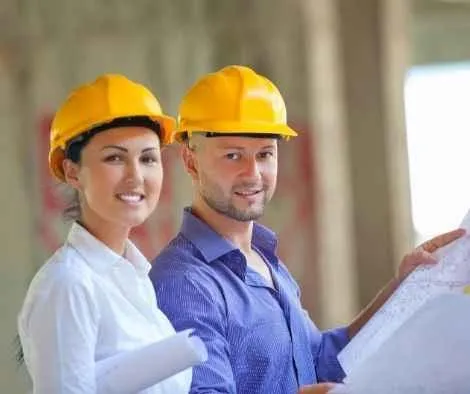
OSHA Plan: Comprehensive OSHA Standards for Compliance
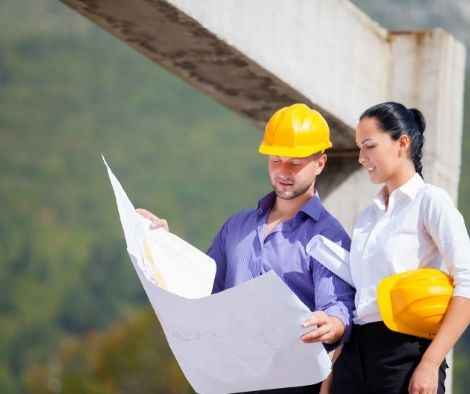
When it comes to workplace safety, compliance isn't just a choice—it's a necessity. Every business needs a solid OSHA Plan to ensure the safety of their employees, meet regulatory standards, and protect the organization from potential legal and financial risks.
By incorporating the right strategies and practices into your plan, your business can stay compliant while fostering a culture of safety. In this post, we’ll walk you through the critical steps in building an effective Accident Prevention Plan OSHA that aligns with OSHA Standards for Accident Prevention, helping your company stay compliant and safe.
With the right tools in place, your team will be equipped to identify, address, and prevent workplace hazards before they become a problem.
Why OSHA Plans Matter for Accident Prevention
An OSHA Plan serves as your blueprint for creating a safer, more compliant workplace. The Occupational Safety and Health Administration (OSHA) has set strict guidelines to help employers prevent accidents and injuries, but the responsibility to meet these standards rests with you.
Not only does a solid OSHA Plan help you avoid costly fines, but it also ensures the well-being of your workforce, fostering a culture of safety that can enhance employee morale and productivity. A compliant workplace helps reduce the risk of accidents, limiting downtime, healthcare costs, and potential legal ramifications that can arise from non-compliance.
Moreover, an effective Accident Prevention Plan OSHA isn't just about protecting your employees, it's about building trust and ensuring that every team member goes home safe at the end of each day. A well-implemented OSHA plan builds a foundation for long-term success, enabling your company to focus on growth while prioritizing safety at every level.
OSHA Standards for Accident Prevention: What You Need to Know
Understanding OSHA’s guidelines is the first step in developing your Accident Prevention Plan OSHA. These standards are designed to protect workers from hazards, and they vary based on the industry and nature of the work being performed.
By adhering to OSHA Standards for Accident Prevention, you create an environment that actively reduces risks.
Here's a breakdown of the key elements you need to incorporate into your OSHA Plan to stay compliant:
General Duty Clause:
Employers are required to provide a workplace free from recognized hazards that could potentially harm workers. This clause is broad and can apply to almost every aspect of your business operations, from the layout of the workspace to the machinery being used. It requires employers to ensure a safe work environment by identifying and addressing safety hazards.
Specific Industry Regulations:
OSHA has developed regulations that apply to specific industries such as construction, manufacturing, and healthcare. These guidelines are tailored to the unique risks associated with each sector.
For example, in construction, fall protection and proper scaffolding are critical, while in healthcare, infection control and patient handling protocols are of utmost importance. To be fully compliant, it is essential to understand the OSHA Standards for Accident Prevention specific to your industry.
Workplace Hazard Analysis:
Identifying, assessing, and mitigating risks is one of the most critical steps in an Accident Prevention Plan OSHA. Regular hazard assessments help identify potential dangers that could lead to accidents. These can include physical hazards like machinery malfunctions, chemical exposures, and ergonomic risks. A proper hazard analysis also helps you to anticipate changes in the workplace and make necessary adjustments before a potential accident occurs.
Employee Training:
Ensuring your team is educated about the hazards they face and how to mitigate them is vital. Safety training ensures that employees understand the risks and are well-equipped to handle emergencies when they arise. Training should cover the correct use of personal protective equipment (PPE), emergency procedures, and proper handling of hazardous materials. Additionally, ongoing training should be part of your Accident Prevention Plan OSHA, with regular updates to reflect any changes in OSHA guidelines or the nature of your workplace risks.
By aligning your OSHA Plan with these essential guidelines, your business will not only stay compliant but also establish a comprehensive approach to preventing accidents, ensuring a safer and more efficient work environment.
The best practices for compliance, such as hazard identification and employee education, will serve as the backbone of your Accident Prevention Plan OSHA, minimizing risks and protecting both employees and your business.
Building a Comprehensive OSHA Plan
Creating an OSHA-compliant accident prevention plan doesn’t have to be overwhelming. By breaking the process down into manageable steps, you can create a plan that’s both effective and straightforward.
Below are the critical steps for building your OSHA Plan and ensuring that you meet OSHA Standards for Accident Prevention.
1. Identify Hazards in the Workplace
The first step to building an OSHA-compliant plan is identifying potential hazards. This includes physical hazards (like machinery or toxic chemicals), ergonomic risks, and even psychological hazards like workplace stress. Recognizing these risks is vital to prevent accidents before they happen.
Pro Tip: Regular safety audits and employee feedback can help identify risks you may have overlooked. Engaging with your team allows you to gather different perspectives on potential hazards.
2. Conduct a Risk Assessment
Once hazards are identified, the next step is conducting a thorough risk assessment to determine which ones pose the most danger. This will guide you in prioritizing which risks need immediate attention and which can be monitored over time.
Pro Tip: Use a risk matrix to assess both the likelihood of an accident and the severity of potential injuries. This helps in allocating resources more efficiently, ensuring you focus on the most critical risks first.
3. Create and Implement Safety Policies
After assessing risks, it’s time to create policies and procedures to mitigate those risks. Your Accident Prevention Plan OSHA should include detailed guidelines on how to manage hazards. This should cover emergency procedures, equipment maintenance schedules, and Personal Protective Equipment (PPE) requirements. Having clear policies in place ensures that employees understand what actions to take and when to take them.
4. Provide Employee Training and Education
Even the best plans are useless without proper training. Ensure your employees are well-versed in safety protocols, equipment use, and emergency procedures. Make training sessions regular and comprehensive, with follow-up evaluations to check comprehension.
Training isn’t a one-time event—it’s an ongoing effort that needs to be revisited regularly.
Pro Tip: Interactive training methods, such as safety drills and scenario-based exercises, can make the learning process more engaging and realistic. This helps employees remember key safety practices in case of emergencies.
5. Monitor and Review Your OSHA Plan Regularly
OSHA compliance is an ongoing process. Regular reviews and audits ensure that your plan stays up-to-date with the latest regulations and industry best practices. It’s also a chance to assess the effectiveness of your current plan and make necessary adjustments. If your workplace evolves or new hazards emerge, your OSHA Plan must evolve with it.
By following these steps, you can build a comprehensive OSHA Plan that helps you manage workplace hazards effectively and stay in line with OSHA Standards for Accident Prevention.
Regular updates and evaluations of the plan ensure your workplace remains safe and compliant, making it a space where employees can work with confidence, knowing that their safety is a top priority.
Ensuring Compliance: Your Responsibilities
Incorporating OSHA standards into your safety strategy isn’t just about checking boxes. It’s about fostering a culture of safety where employees feel empowered to work with confidence, knowing they are protected. As an employer, your responsibilities extend beyond just implementing safety procedures.
You must continuously promote safety awareness and integrate OSHA’s Accident Prevention Plan OSHA standards into everyday operations. By actively involving your workforce in safety initiatives, you help create an environment where safety becomes second nature, not just a set of rules to follow.
Your OSHA Plan should be an evolving document, continuously refined to meet the changing needs of your workforce and workplace conditions. It's essential to integrate regular safety meetings and open communication channels, allowing your team to voice concerns and report hazards. Through this, you actively build a safety-first mindset that encourages employees to be vigilant and proactive about their well-being.
Documentation and Recordkeeping: A Critical Element
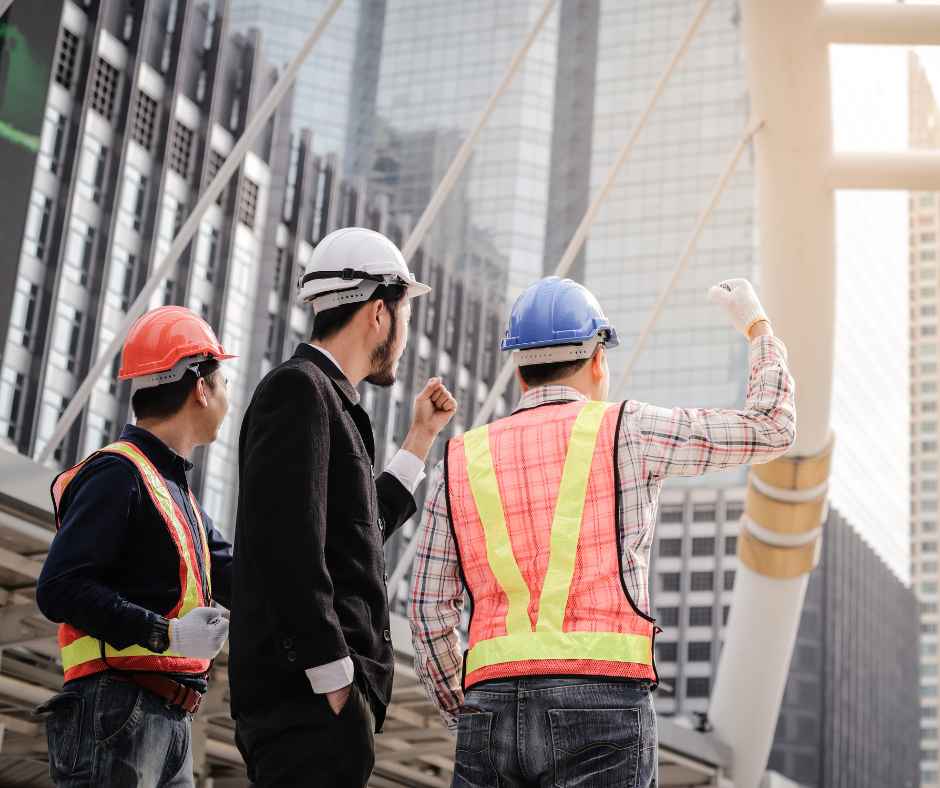
One of the most important responsibilities in maintaining compliance with OSHA Standards for Accident Prevention is diligent documentation. Keep meticulous records of safety meetings, inspections, training, and incidents. These records not only help maintain compliance, but they also serve as evidence in case of an audit.
Documentation provides a trail that demonstrates your commitment to safety and proves that you’ve made necessary efforts to address hazards.
Your Accident Prevention Plan OSHA should include organized records of the following:
Safety Training Logs: Track when employees have undergone training and refresher courses.
Inspection Reports: Document all inspections performed, including hazard assessments and the resulting corrective actions.
Incident Reports: Record any incidents or near-misses that occur, along with the steps taken to prevent recurrence.
Having these records readily accessible is essential during an OSHA audit or inspection, and it can be the deciding factor in ensuring your company is viewed as compliant.
Staying Updated with OSHA Standards
OSHA Standards evolve over time, so it's crucial to stay informed about any changes that may affect your plan. Regularly visit the OSHA website or subscribe to updates to ensure your plan remains compliant with the latest regulations.
Compliance isn’t static—it’s an ongoing effort that requires your attention to any amendments or new requirements.
Additionally, industry-specific changes may impact your Accident Prevention Plan OSHA, as standards often differ depending on the work environment. For instance, construction companies may see changes in fall protection regulations, while healthcare providers may see updates to PPE requirements.
By staying up-to-date, you can make proactive adjustments, ensuring your employees remain protected, and your company stays aligned with OSHA standards.
The commitment to remaining informed also means engaging in continuous professional development. Participate in safety seminars, workshops, or certifications that help your leadership team stay knowledgeable about the latest safety practices and regulations. Implementing an evolving, informed OSHA Plan not only ensures compliance but strengthens the safety culture within your workplace.
Conclusion
Creating a comprehensive OSHA Plan that includes OSHA Standards for Accident Prevention and an Accident Prevention Plan OSHA is essential for maintaining a safe and compliant workplace. This plan not only helps you avoid costly fines and legal issues but also plays a pivotal role in ensuring the safety and well-being of your workforce.
Implementing a well-structured OSHA Plan demonstrates a proactive approach to mitigating workplace hazards and protecting employees from injuries and accidents. It’s a commitment to not just meet legal requirements but to go above and beyond to provide a secure working environment for all.
By following the steps outlined in this post, you can ensure that your organization not only meets legal obligations but also fosters a culture where safety is a priority. Involving employees in safety initiatives, providing consistent training, and encouraging open communication about hazards all contribute to a more engaged and safety-conscious workforce.
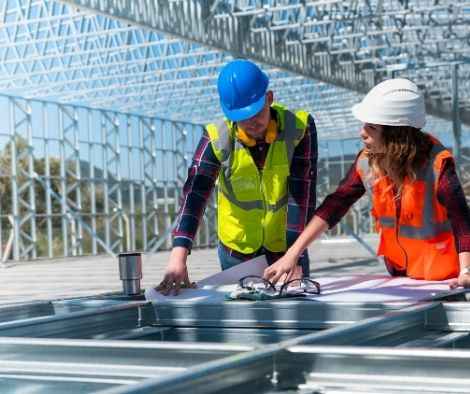
A strong Accident Prevention Plan OSHA leads to greater employee morale and higher productivity, as workers feel secure and valued in their roles.
Remember, workplace safety is a continuous process—stay proactive, involve your team, and always be prepared to adapt to changes in OSHA standards or workplace conditions.
Regular audits, ongoing education, and responsive leadership will help maintain a robust safety culture that not only meets compliance standards but also becomes ingrained in your company's values.
Your business’s success is not only measured by how much it grows but by how safely it operates. A safe work environment enhances employee retention, boosts morale, and minimizes costly downtime due to injuries.
Keep that in mind, and build a safety-first mindset that will pay dividends for years to come. With an effective OSHA Plan, you’ll not only protect your workforce but also create an environment that supports sustained growth, productivity, and a lasting commitment to employee well-being.
If you have any questions, please feel free to contact us. Our professionals have decades of experience and can point you in the right direction and path to success.