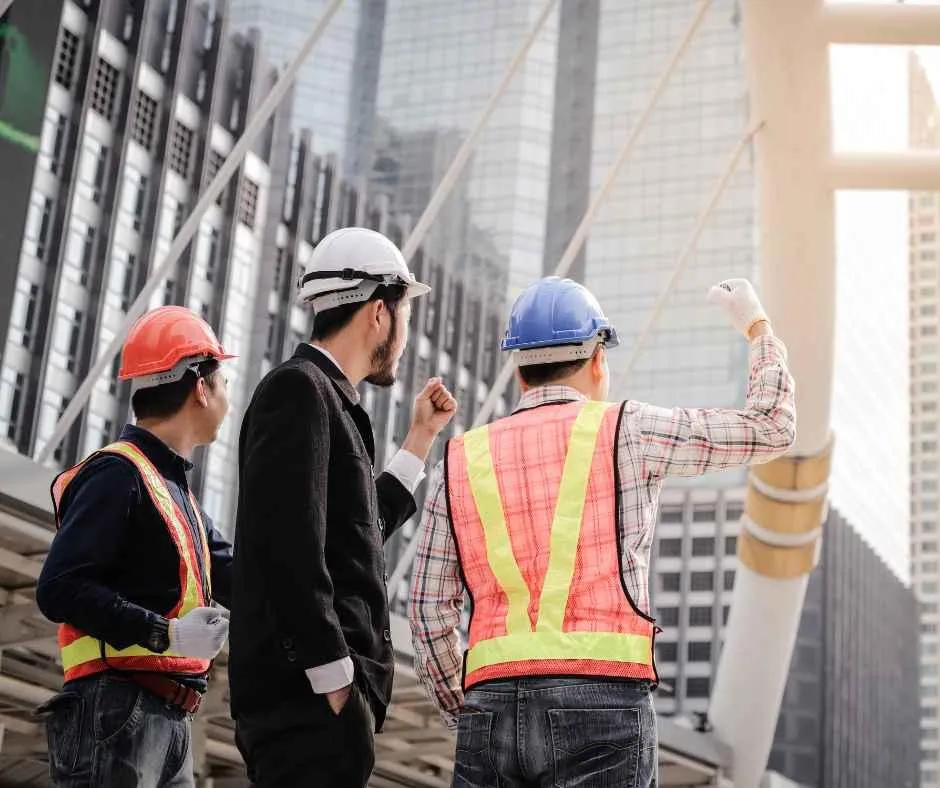
Streamlining Demolition: Key Safety Considerations
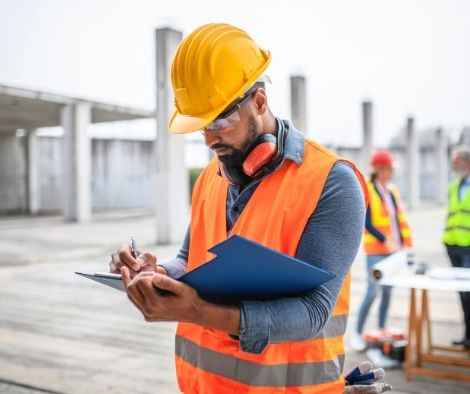
Demolition projects can be complex, requiring precise planning to keep workers safe and ensure the job is completed efficiently. Without a solid demolition plan, risks increase, leading to costly delays or accidents. Whether you're tearing down a small structure or a large commercial building, having a clear approach is essential. Proper demolition plans not only guarantee safety but also help streamline the entire construction process, ensuring all necessary procedures are followed.
In addition to the physical demands of demolition, itβs crucial to account for environmental and structural factors that might impact the project. For example, evaluating hazardous materials like asbestos or lead-based paint must be included in the initial demolition plans to ensure compliance with environmental regulations. Demolition projects also require thorough risk assessments, site inspections, and coordination with utility companies to disconnect services like electricity, gas, and water.
These precautions reduce the potential for accidents, ensuring that workers are aware of any risks in advance. Additionally, a strong demolition plan should address waste management protocols, from sorting recyclable materials to ensuring proper disposal of debris. Taking these extra steps not only maintains safety but also minimizes disruptions to the surrounding area, which can be critical in urban environments.
Why a Strong Demolition Plan Matters
Before breaking ground, a well-thought-out demolition plan is the foundation for a smooth project. It ensures safety protocols are in place, helps mitigate unexpected risks, and keeps the project on schedule. In construction, a strong demolition plan not only provides a roadmap for the work ahead but also outlines crucial elements such as proper sequencing and resource allocation.
A comprehensive plan anticipates challenges like structural integrity, hazardous materials, and potential environmental impacts. It allows project managers to prioritize tasks, allocate labor effectively, and avoid costly delays.
In demolition projects, adherence to local regulations and compliance with safety standards is paramount, making a clear plan essential for staying on track. With all aspects of demolition addressed in advance, teams can work efficiently, minimize disruptions, and ensure that all safety measures are upheld throughout the process, reducing the risk of accidents and injuries on the job site.
Essential Safety Considerations for Demolition Projects
Conduct a Site Assessment
A thorough site assessment identifies structural weaknesses, hazardous materials, and surrounding environmental concerns. Before demolition begins, engineers should inspect the building to determine:
The condition of load-bearing walls and support structures.
Presence of asbestos, lead, or other hazardous materials.
Nearby structures or underground utilities that could be impacted.
A complete site assessment can help minimize risk and ensure compliance with safety standards. Itβs important to assess potential hazards that could cause delays, such as underground utilities or old, poorly supported walls.
By understanding the full scope of the site, construction professionals can plan the demolition accordingly, ensuring it is done safely and efficiently. Utilizing advanced tools like drones for aerial inspection allows for a broader, more thorough view of the site, giving the demolition team valuable insights into potential risks.
Pro Tip: Use drone technology for aerial inspections to gain a comprehensive view of the site before demolition.
Develop a Step-by-Step Demolition Plan
A demolition plan outlines each phase of the project, including:
Method of Demolition: Mechanical, manual, or implosion.
Equipment & Machinery: Excavators, bulldozers, and safety gear required.
Waste Disposal Strategy: Ensuring debris removal follows environmental regulations.
Having a detailed demolition plan ensures that each phase is executed without delay and prevents surprises on the job site. The plan should consider safety measures and potential environmental impacts, such as hazardous material removal or waste management.
Collaborating with a multidisciplinary team, including engineers and safety officers, allows for better planning and mitigation of risks, ensuring all parties are aligned on safety protocols. A well-structured plan also aids in streamlining communication among contractors, enhancing the efficiency of demolition projects.
Pro Tip: Involve all stakeholders, including engineers, safety officers, and contractors, when developing the demolition plan to address potential risks early.
Secure Necessary Permits and Compliance
Construction and demolition projects must adhere to legal regulations. Before beginning work:
Obtain demolition permits from local authorities.
Follow OSHA safety standards and guidelines.
Ensure proper disposal of hazardous materials per EPA regulations.
Adhering to legal and environmental standards is critical to avoid delays, fines, or legal complications. Obtaining permits ensures that all necessary checks are in place, including safety, environmental concerns, and structural integrity. When working on demolition projects, staying compliant with OSHA standards not only ensures safety but also fosters a professional image.
Proper disposal of hazardous materials such as lead, asbestos, or chemicals is paramount in protecting both workers and the environment. Keep thorough records to track compliance with local and federal regulations to avoid penalties.
Pro Tip: Neglecting compliance can result in hefty fines and project delays, so thorough documentation is crucial.
Implement Strict Safety Measures
Safety is paramount in demolition projects. Implement the following measures:
Personal Protective Equipment (PPE): Hard hats, gloves, steel-toed boots, and respirators.
Controlled Demolition Zones: Establish barriers to keep unauthorized personnel away.
Emergency Response Plan: Have a strategy in place for accidents or structural failures.
The safety of workers and nearby residents should always be a priority. Beyond basic PPE, consider safety training that teaches workers how to handle specific demolition tasks, including working with hazardous materials, dealing with falling debris, and navigating unstable structures.
Protective barriers and signage help prevent accidents by clearly marking hazardous areas. Having an effective emergency response plan in place ensures that workers can act swiftly in case of accidents, ensuring quick medical attention if needed. Properly training staff to follow these safety measures reduces the chances of accidents and injuries during demolition.
Pro Tip: Implementing proper emergency evacuation drills can also help prepare workers for any unforeseen circumstances.
Use the Right Demolition Equipment
Using appropriate equipment enhances efficiency and safety. Some common tools include:
The choice of demolition equipment can impact the overall safety and efficiency of the project. Each piece of equipment should be selected based on the type and size of the structure being demolished. Equipment should be maintained regularly to ensure it functions properly and minimizes the risk of mechanical failure during the demolition.
Additionally, advanced machinery such as hydraulic shears can help reduce human error by performing precise cuts, while dust suppression systems prevent the spread of debris and harmful particles into the air, improving visibility and health safety on-site.
Pro Tip: Selecting the right machinery can streamline the demolition process and significantly enhance overall site safety.
Prioritize Environmental and Waste Management
Demolition generates large amounts of debris, making proper waste disposal essential. Best practices include:
Sorting materials for recycling (wood, concrete, metal).
Using dust control measures to minimize air pollution.
Disposing of hazardous waste properly to prevent environmental harm.
Environmental considerations are a key part of modern demolition. Properly sorting recyclable materials such as wood, metal, and concrete can reduce landfill waste and lower disposal costs. By adhering to waste management protocols, you can not only avoid potential fines but also contribute to sustainable construction practices.
Dust control measures like water sprays and air filtration systems should be employed to protect workers' respiratory health and reduce the spread of airborne debris. Additionally, proper hazardous waste management ensures compliance with EPA standards and reduces the risk of contamination.
Pro Tip: Partner with local recycling facilities to reduce landfill waste and lower costs.
Ensure Worker Training and Communication
Workers should be well-trained on demolition safety protocols, including:
Recognizing structural weaknesses.
Handling hazardous materials safely.
Emergency response procedures.
Clear communication and ongoing training are essential for a safe demolition project. Workers should be educated on the potential risks specific to the demolition site and equipped with knowledge on how to identify structural vulnerabilities.
Regular safety meetings can reinforce the importance of PPE usage and other safety protocols. Furthermore, establishing a clear communication system ensures that workers can quickly report hazards or unsafe conditions, making it easier to address issues before they escalate into accidents. Encouraging an open line of communication fosters a culture of safety.
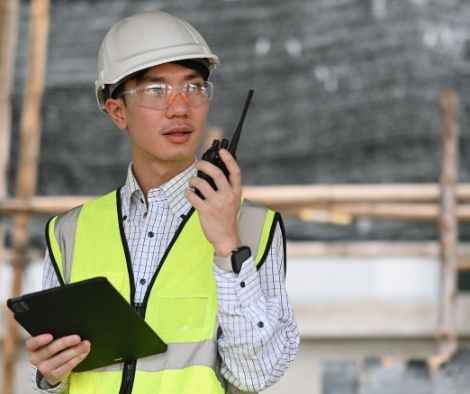
Pro Tip: Daily safety briefings can significantly enhance on-site safety and help workers stay focused on best practices.
Monitor Structural Stability During Demolition
Unexpected collapses are one of the biggest risks in demolition projects. Regularly assess structural integrity by:
Using sensors to detect stress points.
Implementing gradual demolition instead of sudden dismantling.
Keeping emergency exits clear in case of structural failure.
One of the primary concerns during demolition is the risk of an uncontrolled collapse. To mitigate this risk, project managers should monitor the structural stability regularly, using tools like sensors and load monitors to detect stress points that may signal failure.
Gradual and controlled demolition techniques should be employed to avoid sudden, catastrophic collapses. Additionally, all workers should be well-versed in emergency evacuation procedures, with clearly marked exits in place. Keeping emergency exits clear at all times ensures quick access to safety if needed.
Pro Tip: Regular checks using state-of-the-art monitoring equipment can help prevent unforeseen collapses and ensure the site's safety.
Manage Noise and Vibration Impact
Demolition work often causes significant noise and vibrations, affecting nearby properties. To minimize disruptions:
Use sound barriers to reduce noise pollution.
Monitor vibrations to prevent damage to surrounding structures.
Notify neighbors about the demolition timeline in advance.
To reduce the impact of noise and vibrations on surrounding communities, demolition teams should use soundproofing techniques and vibration-dampening equipment. Sound barriers such as walls, fencing, or acoustic blankets can help keep noise levels down, minimizing disruption to nearby businesses and residences.
Monitoring vibration levels ensures that nearby structures arenβt damaged during the process. Itβs also good practice to notify local residents and businesses about the demolition timeline so they can prepare for potential disturbances.
Pro Tip: Proper communication with neighbors before the project begins can prevent complaints and promote a more harmonious working environment.
Post-Demolition Site Cleanup and Inspection
Once demolition is complete, the site must be cleared and inspected. Steps include:
Debris Removal: Ensure all waste is disposed of correctly.
Soil Testing: Check for contamination before new construction begins.
Final Safety Review: Inspect the site to confirm it's hazard-free.
After demolition, itβs essential to carry out a thorough site cleanup to ensure that no hazardous debris is left behind. This includes removing concrete, metal, wood, and any other materials that could pose a risk to workers or the surrounding environment. Soil testing should be performed to confirm that no contaminants, such as chemicals or asbestos, remain in the soil.
A final safety review with the project team helps ensure that the site is completely hazard-free before any new construction begins.
Pro Tip: Conduct a final safety walkthrough with the project team to verify that all debris and hazards have been addressed.
Conclusion
A well-executed demolition plan is the key to ensuring safety, efficiency, and regulatory compliance. By carefully assessing the site, selecting the right equipment, and enforcing strict safety measures, demolition projects can be streamlined with minimal risks. Whether working on a small-scale teardown or a large commercial demolition, prioritizing these key considerations will lead to a smoother, safer, and more cost-effective process.
By following a comprehensive demolition plan, construction teams can reduce unnecessary delays, avoid accidents, and ensure that all legal requirements are met. The inclusion of clear, step-by-step instructions and a focus on worker training is essential to maintaining high safety standards throughout the process. It's also vital to consider post-demolition steps, such as site cleanup and regulatory inspections, to ensure the site is safe for future development.
Streamlining demolition projects by incorporating detailed plans and safety measures not only leads to better project outcomes but also fosters a culture of responsibility and environmental sustainability on construction sites. For information on a full-service writing team to support you in completing your demolition plan, or remediating a denied demolition plan, contact us at Plan The Job for more information on how we can support you.