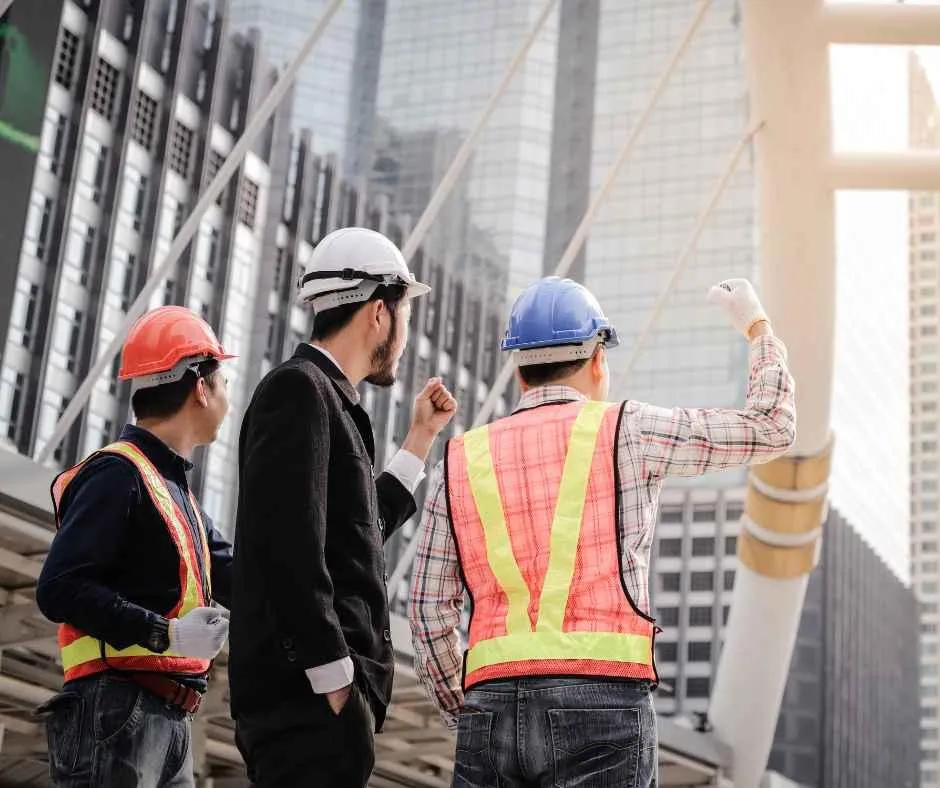
USACE Accident Prevention Plan Guidelines for Contractors
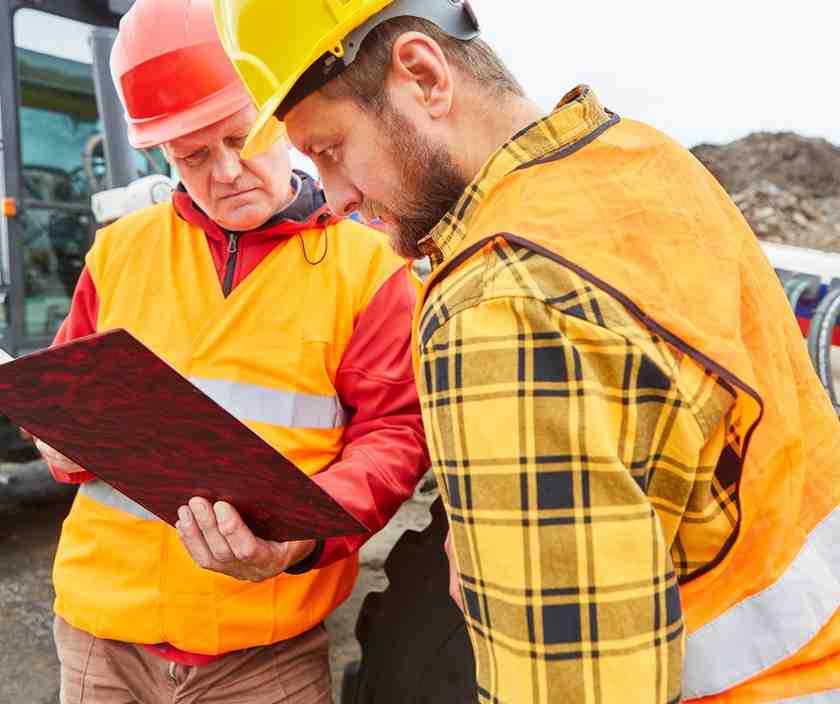
Safety is the foundation of every successful construction project, and when working under the stringent requirements of the U.S. Army Corps of Engineers (USACE), it becomes even more critical.
At the heart of USACE's safety standards is the Accident Prevention Plan (APP)—a detailed framework designed to safeguard workers, minimize risks, and ensure compliance on construction sites.
For contractors, the Accident Prevention Plan is more than a checklist—it’s a roadmap to a safer, more efficient work environment. By understanding its key components and applying proven accident prevention strategies, contractors can create safer sites, reduce incidents, and keep projects running smoothly.
This guide dives into the essentials of the Accident Prevention Plan for construction sites, breaking down its core guidelines and sharing actionable insights. Whether you’re preparing an APP for the first time or enhancing an existing one, you’ll find practical tips to align with USACE standards while prioritizing the safety and well-being of everyone on-site.
Let’s explore how to build an effective Accident Prevention Plan that meets compliance requirements and sets your project up for success.
What Is the USACE Accident Prevention Plan?
The USACE Accident Prevention Plan (APP) is a detailed and structured document required for all contractors working on U.S. Army Corps of Engineers (USACE) projects. Its primary purpose is to identify potential hazards on construction sites and outline clear, actionable measures to mitigate those risks. By doing so, the APP ensures worker safety, compliance, and efficient project execution.
This Accident Prevention Plan for Construction Sites is an essential element of USACE contracts. Contractors are mandated to develop and submit the plan before commencing any work, demonstrating compliance with EM 385-1-1, the USACE Safety and Health Requirements Manual.
This manual outlines the safety protocols and standards that every project must meet to minimize risks and ensure operational success.
A well-prepared Construction Accident Prevention Plan doesn’t just address regulatory requirements—it also establishes a safety-first culture. By proactively managing hazards, contractors can reduce workplace injuries, avoid costly delays, and enhance the overall productivity of the site.
Key Elements of an Effective Accident Prevention Plan
To comply with USACE standards, your Accident Prevention Plan must include the following core components. Each element is essential to ensure worker safety, regulatory compliance, and a proactive approach to managing site-specific risks.
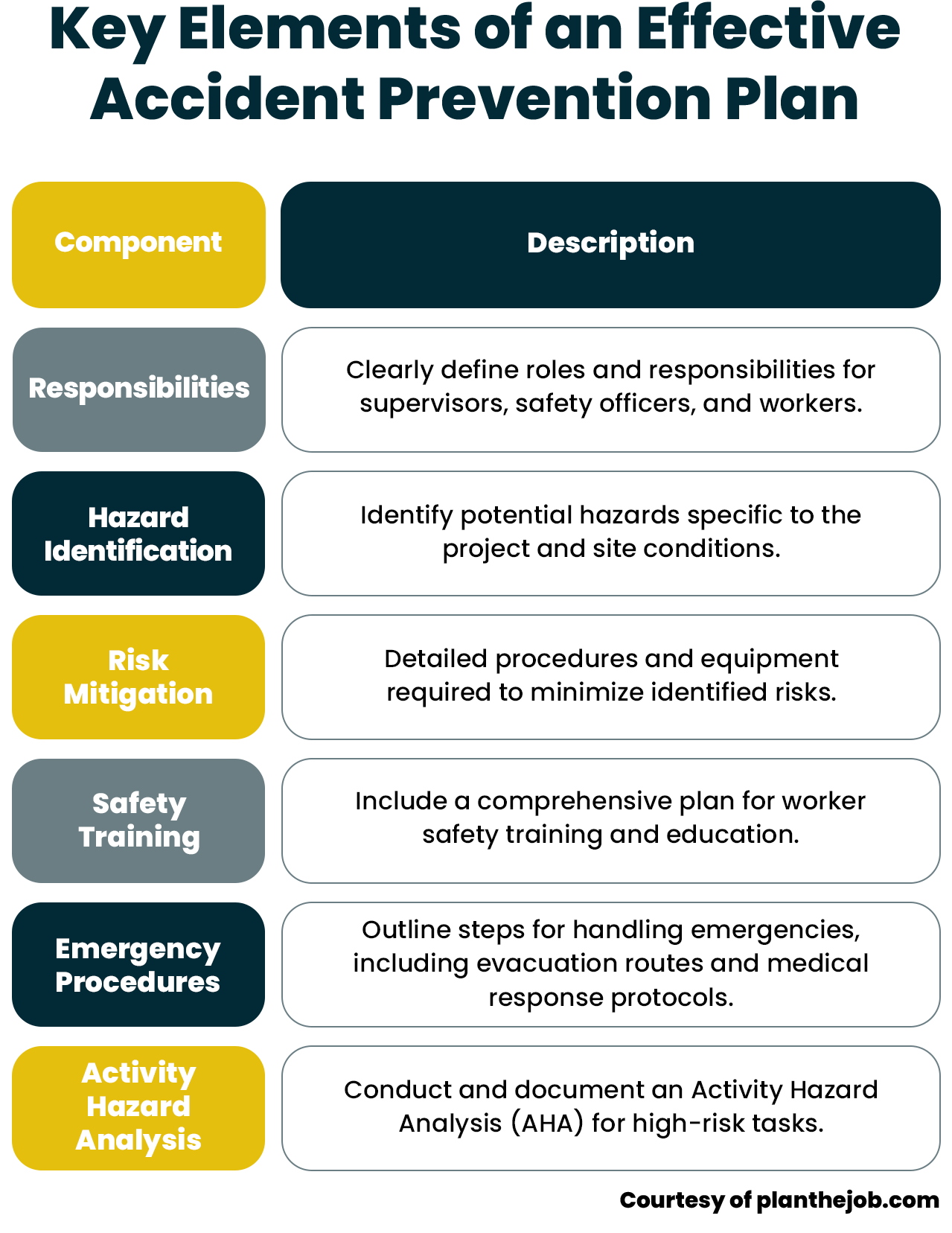
Detailed Breakdown of Each Component
Responsibilities
Assign specific safety tasks to team members, ensuring no aspect of the Construction Accident Prevention Plan is overlooked.
Supervisors should oversee daily implementation, while safety officers should perform routine inspections and audits.
Workers must adhere to the safety practices outlined in the Accident Prevention Plan for Construction Sites and report hazards promptly.
Hazard Identification
Conduct a thorough site walkthrough to identify risks such as tripping hazards, unstable ground, or machinery malfunctions.
Consider environmental factors like extreme weather or proximity to water when assessing hazards.
Use checklists to ensure no potential risk is missed during inspections.
Risk Mitigation
Provide detailed protocols for using safety equipment such as harnesses, hard hats, and gloves to minimize injuries.
Include strategies like scheduling hazardous activities during off-peak hours to reduce worker exposure.
Implement clear signage around high-risk areas to warn workers of potential dangers.
Safety Training
Offer role-specific training sessions to address the unique safety needs of supervisors, equipment operators, and general laborers.
Incorporate hands-on demonstrations to ensure workers fully understand proper safety practices.
Maintain training records for accountability and compliance with USACE standards.
Emergency Procedures
Designate a safety officer to oversee emergency drills and ensure workers are familiar with evacuation routes.
Equip the site with first-aid kits, fire extinguishers, and an emergency communication system.
Establish a clear reporting protocol for accidents, including immediate notification of site supervisors and USACE representatives.
Activity Hazard Analysis (AHA)
Break down each high-risk activity into specific tasks and assess potential hazards for each.
Document control measures and ensure they are communicated to the team before work begins.
Regularly review and update AHAs to reflect changing site conditions or new risks.
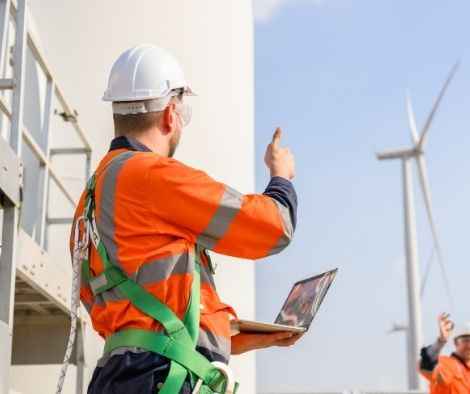
Enhancing Your Plan with Accident Prevention Strategies
To ensure your Effective Accident Prevention Plan meets USACE requirements, consider integrating additional Accident Prevention Strategies, such as:
Conducting regular safety meetings to address new or emerging risks.
Establishing a safety committee to promote worker involvement in risk management.
Using technology like wearable safety devices to monitor worker health and safety in real-time.
Encouraging a culture of safety where workers feel empowered to report hazards without fear of retribution.
These detailed steps and strategies ensure your Accident Prevention Plan for Construction Sites is not only compliant but also a practical tool for maintaining a safe and productive work environment.
Developing an Accident Prevention Plan for Construction Sites
An Accident Prevention Plan tailored for construction sites must address the unique challenges posed by such environments. Construction sites are dynamic, with multiple potential risks, so a comprehensive, site-specific approach is crucial.
Below are the steps to create an Effective Accident Prevention Plan:
Assess the Site and Project Scope
Every construction site has its own set of risks, influenced by terrain, project specifics, and the tools used. Start by performing a thorough site assessment to identify:
Terrain-specific hazards, such as uneven ground, steep slopes, or proximity to water bodies. These environmental factors can significantly impact worker safety and require special precautions such as proper ground stabilization and the use of safety barriers.
Project-specific risks, such as working with heavy machinery, excavation tasks, or working at height. Assess the equipment being used on-site and the potential dangers associated with it. For example, working with cranes or forklifts requires clear safety protocols for operating and interacting with these machines.
Traffic patterns, especially if construction involves major roadworks. Workers may be exposed to moving vehicles, so it’s vital to establish clear pathways and signage.
Weather-related risks, such as high winds, rain, or extreme temperatures, which can influence safety measures like the proper attire or equipment necessary for the day’s work.
Incorporate USACE Guidelines
USACE projects require strict adherence to EM 385-1-1 standards, which provide detailed safety guidelines for construction projects. When developing your Accident Prevention Plan for Construction Sites, make sure your APP:
Aligns with the manual’s requirements. These standards encompass a wide range of safety topics, including fall protection, confined space entry, and equipment safety.
Includes procedures for periodic safety audits to ensure compliance with USACE standards throughout the project. Regular audits help identify any gaps in safety protocols or areas where additional precautions may be needed.
Is reviewed and approved by a qualified safety professional who is familiar with the EM 385-1-1 standards. A professional’s expertise ensures that the plan is both comprehensive and tailored to meet the unique needs of the project.
Engage Your Team
Worker involvement is critical for the success of any Accident Prevention Plan. Engaged and well-informed workers are more likely to follow safety protocols and report hazards when they arise.
Host pre-construction safety meetings to:
Explain the APP to all team members, ensuring they understand its importance and their role in maintaining a safe work environment.
Address questions and concerns, allowing workers to voice any uncertainties about safety procedures. Clear communication helps to reduce confusion and ensures everyone is on the same page.
Emphasize the importance of adhering to safety protocols and how they directly contribute to a safer work environment. Reinforce that safety is a shared responsibility among all team members.
Assign specific safety duties, such as appointing safety officers or supervisors to monitor specific activities and ensure compliance with safety standards.
By following these steps, contractors can ensure that their Construction Accident Prevention Plan is not only comprehensive but also aligned with USACE guidelines. The plan should be viewed as a living document, regularly updated and reviewed to address new hazards or changes on the job site.
An Effective Accident Prevention Plan is the foundation for a safe and compliant work environment, and actively engaging with your team is key to ensuring its success.
Pro Tip: Use visual aids like safety posters and diagrams on-site to reinforce key safety messages.
Best Practices for Accident Prevention Strategies
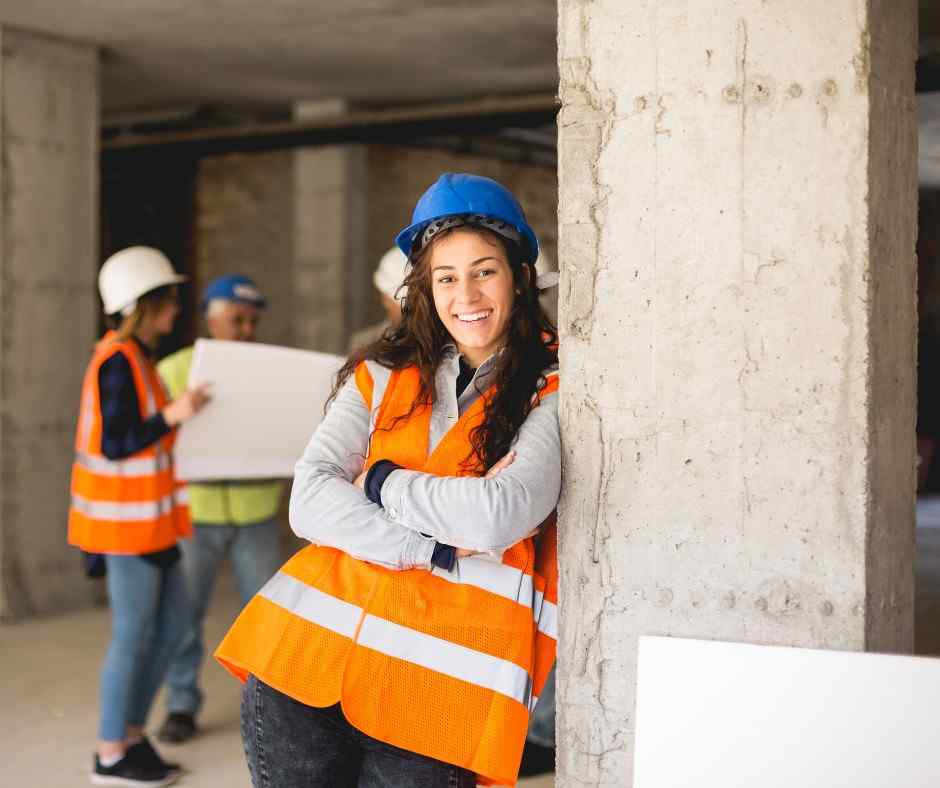
1. Regular Safety Training
Ongoing education ensures that workers remain aware of the latest safety practices. Effective training programs should:
Cover both general and site-specific hazards.
Include hands-on demonstrations for using protective equipment.
Be updated regularly to reflect new risks and regulations.
2. Conduct Routine Inspections
Frequent site inspections help identify potential issues before they become serious. Inspections should:
Be performed daily or weekly, depending on project size.
Focus on high-risk areas and activities.
Involve supervisors, safety officers, and workers.
3. Use Proper Protective Equipment
Ensuring that all workers have access to and use appropriate Personal Protective Equipment (PPE) is a foundational safety measure. Key examples include:
Hard hats, safety goggles, and steel-toed boots.
Harnesses for working at heights.
Respirators for dusty or hazardous environments.
4. Implement an Emergency Response Plan
Even with the best Accident Prevention Plan, emergencies can happen. Prepare your team by:
Establishing clear communication protocols.
Conducting regular drills for evacuation and medical emergencies.
Designating first-aid responders on-site.
Common Pitfalls to Avoid in Your Construction Accident Prevention Plan
Creating an Accident Prevention Plan (APP) is only part of the equation—it must be actionable and effective. To ensure your plan achieves its safety goals, avoid these common mistakes that can undermine its success:
Generic Plans
A one-size-fits-all approach won’t address specific site risks. Each construction site has unique hazards depending on factors such as the environment, project type, and equipment used. It’s essential to customize your Accident Prevention Plan for Construction Sites to reflect these specifics. For example, a site with heavy machinery will have different risks compared to a residential construction site.
Outdated Information
Your APP must be a living document, regularly updated to stay relevant. Changes in the project scope, site conditions, or safety regulations can create new risks. Review and update your Effective Accident Prevention Plan periodically, especially after any significant changes or incidents on-site. Keeping it current ensures it remains effective in preventing accidents and aligns with industry standards.
Lack of Enforcement
Creating an Accident Prevention Plan is futile if it’s not enforced. Supervisors must actively monitor the implementation of safety protocols, ensuring compliance across all stages of the project. A lack of enforcement can lead to neglecting safety measures, increasing the likelihood of accidents. Establish a clear system of accountability, with regular checks and disciplinary actions if necessary.
Insufficient Worker Training
Even the best plan won’t work if workers aren’t properly trained. Ensure your team receives thorough safety training specific to the tasks they will be performing. The training should include hazard recognition, proper equipment usage, and emergency procedures.
Failure to Involve Workers
Workers should be encouraged to report hazards and contribute to the development of safety protocols. Engaging your team fosters a culture of safety and ensures that everyone is invested in the plan's success.
Ignoring Small Hazards
Even seemingly insignificant risks, such as small spills or improper storage of tools, can lead to accidents. Don’t overlook the small stuff—address all hazards, big and small, in your Construction Accident Prevention Plan.
Lack of Clear Communication
Effective communication is key to safety. Make sure safety instructions are clear, concise, and easily accessible to all workers. Signs, labels, and daily safety briefings can help maintain clarity on the job site.
Inadequate Emergency Procedures
A well-developed emergency response plan is crucial for quick action during a crisis. Ensure your Accident Prevention Plan includes clear evacuation routes, first-aid kits, and designated emergency contacts.
Pro Tip: Use software tools to streamline safety reporting and document management, making it easier to keep your APP up-to-date.
How to Evaluate the Effectiveness of Your Accident Prevention Plan
To ensure your APP is doing its job, regularly evaluate its performance by:
Tracking incident reports and near-misses.
Soliciting feedback from workers and supervisors.
Comparing safety metrics against industry benchmarks.
Table: Example Evaluation Metrics for APP Effectiveness
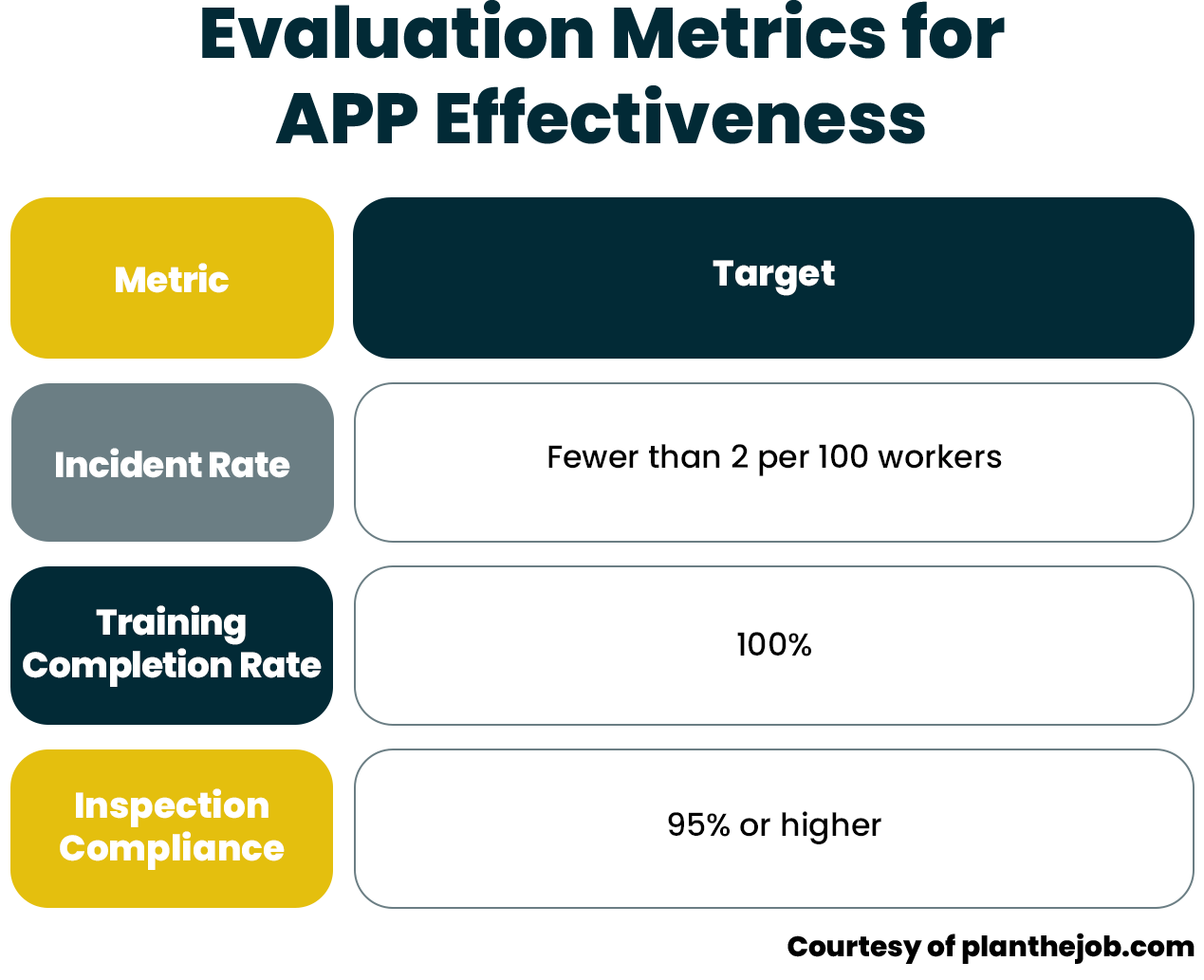
Conclusion
An effective Accident Prevention Plan is more than a regulatory requirement—it’s a vital tool for creating a safe, productive, and compliant work environment. By understanding the key components of the USACE Accident Prevention Plan, tailoring it to the unique challenges of construction sites, and implementing proven accident prevention strategies, contractors can protect their teams and achieve project success.
Remember, safety is everyone’s responsibility. A well-crafted APP sets the foundation for a culture of accountability and care, ensuring that every worker goes home safe at the end of the day.