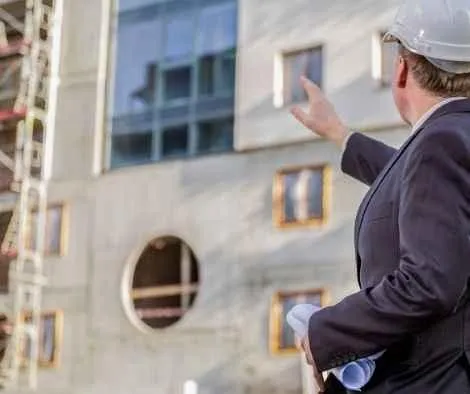
Army Corps Effective Accident Prevention & Injury Plan
When mistakes occur on the job, the outcomes can be serious—ranging from costly delays to life-altering injuries. In sectors where teamwork and precision are key, ensuring safety through proven methods isn’t just an option; it’s a necessity.
This blog post provides actionable strategies that resonate with professionals working with the Army Corps. We’ll explore essential accident prevention strategies, focus on developing an injury illness prevention plan, and outline how the Army Corps of Engineers constantly refines these protocols.
In today’s dynamic operational environment, safety remains the foremost priority. Whether you're on a construction site or in a field setting, adopting systematic safety measures not only protects lives but also drives productivity.
Let’s take a closer look at smart, practical approaches that significantly reduce on-site injuries and accidents.
Understanding the Safety Culture
The Stakes for the Army Corps
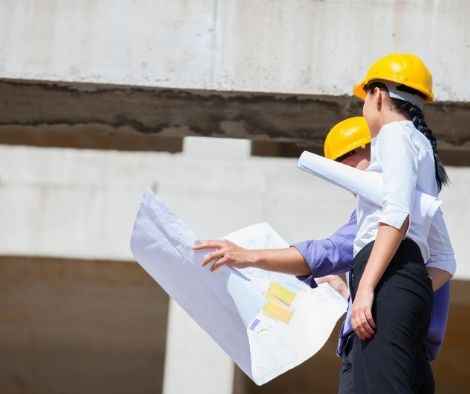
For organizations like the Army Corps, every project requires carefully planned measures to safeguard personnel and property. Incidents often have a domino effect—impacting project timelines, budgets, and worker morale. It is crucial that every team member understands their role in accident prevention and the importance of following established safety protocols.
Key points include:
Team Communication: Regular briefings and open channels for reporting safety concerns.
Rigorous Training: Continuous training sessions to keep safety skills sharp.
Proactive Oversight: Routine audits and updates to safety plans based on the latest field data.
By fostering a culture of accountability and clear communication,Army Corps operations can consistently improve their accident prevention strategies.
Core Components of Accident Prevention Strategies
Accident prevention requires planning, coordination, and ongoing education. Here are some of the most effective strategies:
1. Regular Safety Audits and Inspections
Conducting frequent and thorough audits is a crucial element. Regular inspections help identify hazards before they result in incidents. These reviews should include:
Site Walkthroughs: Inspecting the worksite for potential risks.
Equipment Checks: Ensuring that all machinery and tools meet safety standards.
Incident Analysis: Reviewing past incidents to understand trends and prevent reoccurrence.
2. Continuous Training Programs
Training isn’t a one-time event. Recurrent sessions help keep the safety knowledge fresh for all staff. Training should cover:
Emergency Procedures: What to do if an incident occurs.
Safe Operation of Machinery: Operating equipment within safety protocols.
Hazard Recognition: Identifying and mitigating risks before they escalate.
3. Clear Standard Operating Procedures (SOPs)
SOPs play an essential role in guiding everyday operations. Clear and concise instructions reduce misunderstandings and lower the risk of accidents.
Components of effective SOPs include:
Step-by-step procedures for routine tasks.
Defined roles and responsibilities for each team member.
Emergency response protocols and contact information for immediate assistance.
4. Technology Integration
Modern safety practices increasingly rely on technology. Utilizing software solutions and real-time monitoring systems can significantly enhance safety measures. For instance:
Wearable Sensors: Track worker movement and alert managers to dangerous conditions.
Digital Checklists: Ensure that every safety step is followed without oversight.
Incident Reporting Apps: Immediate reporting and analysis of near-misses and accidents.
5. Employee Engagement and Empowerment
Creating a workplace where employees feel they have a say in safety protocols is invaluable. When workers are actively involved in safety planning:
They are more likely to adhere to procedures.
They provide firsthand feedback, which helps refine prevention strategies.
They contribute ideas to improve overall safety culture.
Building a Comprehensive Injury Illness Prevention Plan
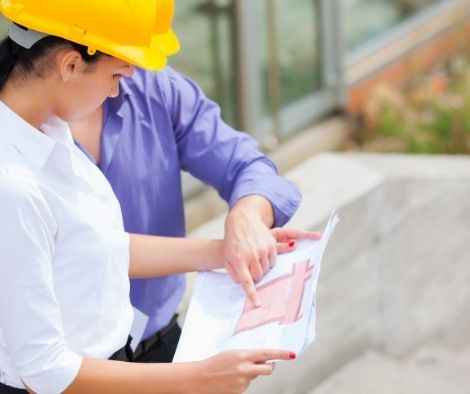
A well-structured Injury illness Prevention Plan is as vital as the accident prevention strategies themselves. It provides a clear roadmap for responding to potential hazards and managing workplace health issues.
Components of a Successful Injury Illness Prevention Plan
Risk Assessment and Management:
Begin with identifying all potential hazards. Establish a risk matrix that categorizes hazards based on their probability and impact. Use this matrix to prioritize interventions.Clear Reporting Channels:
Develop and publicize a simple process for reporting safety concerns and incidents. Ensure that there is an immediate response system in place to address any issues that arise.Regular Training and Drills:
Just as with accident prevention strategies, hands-on training and regular drills are non-negotiable. Practice emergency response procedures often to keep everyone prepared.Documentation and Follow-Up:
Record every incident, no matter how minor, and follow up with a thorough investigation. Detailed documentation helps to reinforce the importance of safety and identify areas for improvement.Employee Health Programs:
Incorporate health and wellness initiatives that promote physical fitness, mental well-being, and overall health. A healthy workforce is a safer workforce.
Army Corps of Engineers: A Case Study in Safety Excellence
The Army Corps of Engineers often finds itself in challenging environments that demand an unwavering commitment to safety. Their approach is built on clear principles that can serve as a model for any large-scale operation.
Here’s a closer look:
Best Practices from the Field
Collaborative Communication: Daily briefings and debriefings keep everyone on the same page.
Up-to-Date Equipment: Regular checks to ensure that all tools and machinery meet modern safety standards.
Adaptive Plans: Using data from recent incidents to continuously refine procedures.
Real-World Impact
Implementing these strategies has shown measurable improvements.
Projects managed under these protocols have experienced:
A notable decrease in accident rates.
Enhanced worker morale and reduced turnover.
Overall improvement in project timelines due to fewer disruptions.
Detailed Implementation: A Step-By-Step Guide
Developing a successful accident prevention and injury illness prevention plan involves multiple phases. Here is a structured approach that can be used by teams and management alike:
Phase 1: Assessment and Planning
Step 1: Conduct a Full Hazard Analysis
Survey current operations.
Identify potential accident sources.
Consult with frontline employees for insights.
Step 2: Develop the Risk Matrix
Create a table categorizing risks based on likelihood and severity.
Prioritize risks to address high-impact issues first.
Step 3: Set Clear Objectives
Define what success looks like in terms of reduced accidents and improved safety compliance.
Establish measurable targets.
Phase 2: Execution
Step 1: Roll Out Training Programs
Schedule and conduct comprehensive training sessions.
Use real-life examples to drive points home.
Step 2: Implement Technology Tools
Adopt wearable sensors and digital reporting systems.
Train employees on the use of these tools.
Step 3: Establish Clear Communication Lines
Set up regular meetings, bulletins, and check-ins.
Empower team leads to monitor compliance and report issues.
Phase 3: Monitoring and Improvement
Step 1: Continuous Monitoring
Set up daily or weekly checklists.
Use periodic audits to track compliance.
Step 2: Data Collection and Analysis
Keep a log of all incidents.
Review data to identify trends and areas for improvement.
Step 3: Adjust Procedures
Update SOPs as needed based on feedback and data analysis.
Hold refresher sessions periodically.
The Human Element in Safety Management
While plans and technology are crucial, the most important part of any accident prevention strategy is the people behind it.
Building a Team-Oriented Environment
Encourage Open Dialogue:
Creating an atmosphere where team members feel comfortable raising concerns is key. Regular safety meetings should invite suggestions for improvement and constructive criticism.Recognize Safe Behaviors:
Implement a recognition system that rewards employees for following safety protocols and reporting potential hazards. Even small acknowledgments go a long way in building commitment.Leadership Involvement:
Leaders must set an example by actively participating in safety training, performing regular site audits, and making safety a core part of company culture.
Addressing Common Challenges
Some common challenges in accident prevention include complacency, communication breakdowns, and resistance to change. Address these challenges by:
Providing Continuous Motivation:
Reinforce the importance of safety with regular updates and success stories.Simplifying Procedures:
Ensure that all protocols are straightforward and easy to follow. Complexity can lead to errors.Setting Clear Expectations:
Every team member should understand their role and the steps required to maintain a safe work environment.
Integrating the Injury Illness Prevention Plan with Daily Operations
It is critical that an injury illness prevention plan is not viewed as a separate entity, but rather as a live part of every daily operation. Here are ways to integrate safety protocols seamlessly:
Daily Safety Briefings
Starting the day with a concise briefing helps set the tone for safety. Key aspects include:
Highlighting any unique risks that day.
Reminding teams of the proper use of personal protective equipment.
Reiterating emergency procedures should an incident occur.
Documentation and Follow-Up
Efficient record-keeping is the backbone of any sound safety plan. Maintain detailed logs that capture:
Daily safety checklists.
Incident reports, no matter how minor.
Feedback from safety meetings and training sessions.
A well-maintained record not only serves to improve future operations but also helps in compliance with regulatory agencies.
Roadmap to a Safer Future
To build a lasting culture of safety within the Army Corps, it is essential to combine planning, training, and a continuous feedback loop. Below is a summary of the roadmap that has proven effective:
Assessment:
Conduct extensive hazard assessments and use risk matrices to prioritize intervention areas.Implementation:
Roll out clear standard operating procedures and recurrent training sessions. Integrate modern technologies for real-time oversight.Monitoring:
Engage in daily reviews and periodic audits. Keep detailed records and adjust plans as necessary.Team Involvement:
Cultivate an environment of open communication and shared responsibility. Encourage team-led initiatives and recognize safe practices.Continuous Improvement:
Use collected data to refine and update safety protocols continuously.
These steps foster a work environment where safety is part of the core operational strategy—minimizing risks while maximizing productivity.
Real-World Examples and Success Stories
Let’s consider a few real-world scenarios where these strategies have had tangible effects:
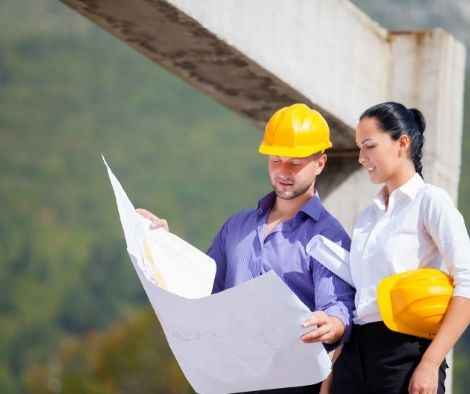
Example 1: Construction Site Safety Overhaul
A large construction project managed by an Army Corps team incorporated daily safety briefings and frequent equipment checks. Over the span of one year, the site experienced a 30% reduction in on-site injuries. Key factors included active team communication and the use of digital safety checklists.
Example 2: Routine Equipment Inspections
In another instance, a mid-scale project implemented a strict schedule for equipment inspections. By identifying small issues before they escalated, the project saw fewer incidents and significantly lower downtime. Adhering closely to a well-documented injury illness prevention plan proved to be highly effective.
Example 3: Employee-Driven Safety Initiatives
An Army Corps team encouraged employees to propose changes to existing safety procedures. This bottom-up approach led to innovative solutions, such as repositioning high-risk equipment and updating emergency procedures based on frontline feedback. The project not only met its safety targets but also boosted morale and efficiency.
Maintaining Momentum
One of the most effective ways to ensure lasting success is to maintain momentum through continuous training and regular feedback loops. Consider hosting quarterly meetings where:
New Safety Measures are introduced.
Feedback from Field Staff is discussed to further refine procedures.
Recent Incident Data is analyzed to provide guidance for further improvements.
This ongoing process builds trust and commitment among employees while keeping safety protocols relevant to evolving operational challenges.
Actionable Tips for Immediate Improvement
For those looking to get started on improving accident prevention in their own operations, here are some actionable tips:
Review and Update: Regularly review your existing safety protocols and update them based on the latest industry standards.
Engage Your Team: Foster an environment where every team member feels responsible for safety.
Implement Checklists: Use daily and weekly checklists to ensure no step in your safety procedures is overlooked.
Invest in Training: Dedicate time and resources to continuous training programs that cover both preventative measures and emergency response.
Use these tips as a starting point. Tailor your approach to fit the specific needs of your operations and regularly measure the success of your initiatives.
Conclusion
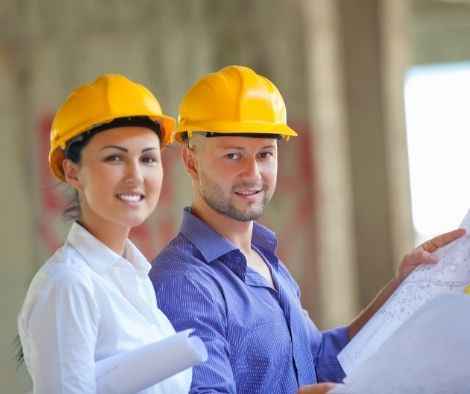
The safety of your workforce is the cornerstone of operational success. By adopting comprehensive accident prevention strategies and a robust injury illness prevention plan, teams can minimize risks while ensuring a productive work environment. The practices outlined in this post are designed to be implemented immediately and maintained through regular training, feedback, and continuous improvement efforts.
Through an unwavering commitment to safety, the Army Corps and similar teams set a high standard for the industry. These strategies not only protect lives and assets but also build a legacy of trust, responsibility, and excellence in every project undertaken.
Call to Action
Get Started with Professional Safety Assessments: Secure immediate evaluation services for your project sites.
Request a Detailed Safety Protocol Review: Enjoy expert guidance on accident prevention strategies and injury illness prevention plan enhancements.
Secure Our Proven Solutions: Experience peace of mind by applying our step-by-step approach, refined by experts familiar with Army Corps operations.
Contact Us Now – No Obligation: Reach out via our website for fast, risk-free consultations on optimizing your site safety measures.
Request a free consultation—No obligation, No risk.
Take the first step toward a safer and more efficient operational future. Your team’s safety is our top priority—act now and secure expert support for immediate improvements.