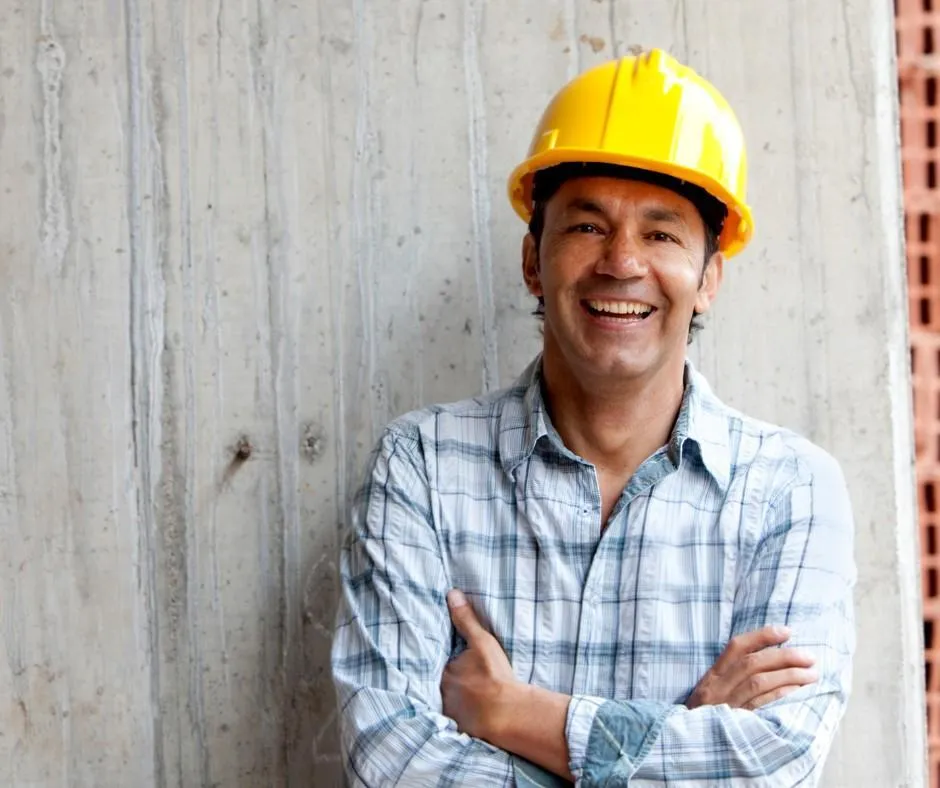
Quality Control Plan for Construction: 100% Approved
A robust construction quality control plan is the backbone of successful projects in the construction industry. It ensures that every phase, from design through execution, meets the rigorous standards expected by clients, regulators, and oversight bodies such as USACE and NAVFAC.
In the construction industry, quality control is not just an administrative requirement—it’s a commitment to safety, reliability, and performance. A well-written quality control plan outlines procedures, responsibilities, and metrics that guarantee the work meets both client expectations and regulatory standards.
Without such a plan, projects risk delays, rework, increased costs, and even safety issues. This guide is especially valuable for professionals aiming to secure 100% approval from entities like USACE and NAVFAC.
Quality control plans serve multiple purposes: they provide a roadmap for the entire project, help manage risks, and ensure that any deviations from the expected outcomes are promptly addressed.
In an era where construction projects are increasingly complex, having a clear, structured quality control plan is more important than ever.
Why Quality Control Plans Get Rejected
Despite their importance, many quality control plans are rejected. Understanding the common reasons behind these rejections is the first step to ensuring that your plan gets approved without hitches.
Lack of Clear Objectives and Scope
One of the most frequent pitfalls is failing to clearly define the objectives of the quality control plan. Without well-articulated goals, stakeholders may question the plan’s purpose and its alignment with project requirements.
Ambiguous Goals: Plans that do not specify measurable quality objectives or benchmarks often leave room for interpretation, leading to inconsistencies.
Undefined Scope: A plan that lacks detailed scope may omit critical processes or responsibilities, which results in incomplete coverage of the construction project.
Insufficient Detailing of Procedures and Standards
Quality control in construction requires a high level of detail. Many plans are rejected because they gloss over important procedural details.
Generic Procedures: Using a one-size-fits-all approach without tailoring the plan to the specific project can signal a lack of understanding of unique project challenges.
Missing Standards: Failing to reference industry standards, including those specific to USACE and NAVFAC, undermines the credibility of the plan.
Poor Documentation and Record-Keeping
Effective quality control relies heavily on documentation. If the plan does not clearly outline how data will be recorded and monitored, reviewers will doubt its reliability.
Incomplete Records: A lack of robust documentation procedures can lead to gaps in tracking project quality, making it difficult to identify and resolve issues.
Inadequate Reporting Mechanisms: Plans that do not include regular reporting or audits tend to fall short in maintaining continuous quality oversight.
Overlooking Risk Management
Construction projects are fraught with potential risks. Plans that fail to incorporate risk management strategies are often rejected.
Absence of Contingency Measures: A quality control plan must address potential risks and provide clear contingency measures to mitigate them.
Reactive Rather Than Proactive: Quality plans that only react to problems rather than anticipating them are typically seen as insufficient.
Non-Compliance with Regulatory and Client Requirements
Every construction project must adhere to specific regulatory and client mandates. Quality control plans that overlook these requirements are destined for rejection.
Ignoring USACE/NAVFAC Standards: When a plan does not meet the specialized requirements of governing bodies like USACE or NAVFAC, it automatically becomes non-compliant.
Failure to Align with Client Specifications: If the plan does not reflect the detailed quality expectations of the client, it will likely be seen as inadequate.
How to Structure a Plan That Meets USACE/NAVFAC Standards
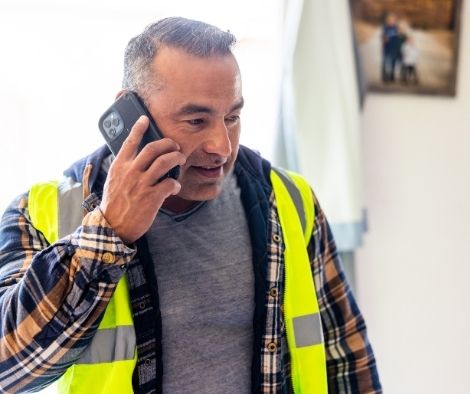
Creating a quality control plan that meets the high standards of USACE and NAVFAC requires a structured, systematic approach. Here are the essential components:
1. Executive Summary
Begin your plan with an executive summary that provides an overview of the project, the quality control objectives, and the key elements of the plan. This section should be succinct yet comprehensive, offering a snapshot of what the plan aims to achieve.
Project Overview: Briefly describe the construction project, including key milestones and expected outcomes.
Quality Objectives: Clearly state the quality targets, benchmarks, and performance indicators.
Key Personnel: Identify the individuals responsible for quality control, including their roles and responsibilities.
2. Detailed Scope and Objectives
Outline the specific areas of construction that the quality control plan will cover. This section should detail what is included—and importantly, what is excluded—to avoid any misunderstandings later on.
Scope of Work: Define the boundaries of the quality control plan, highlighting all critical construction phases.
Quality Objectives: Include specific, measurable, achievable, relevant, and time-bound (SMART) objectives.
Deliverables: List the quality control deliverables expected at each stage of the project.
3. Quality Control Processes and Procedures
This is the heart of the plan. Detail the processes, methodologies, and procedures that will be used to maintain quality throughout the project.
Inspection and Testing: Outline the inspection schedule and the types of tests that will be conducted, including in-process inspections and final evaluations.
Material Control: Describe how materials will be checked, approved, and tracked to ensure they meet project specifications.
Workmanship Standards: Define the criteria for workmanship, including the acceptable tolerances and performance metrics.
Documentation and Reporting: Explain how quality data will be collected, stored, and reported. Regular audits and reviews should be scheduled to ensure ongoing compliance.
4. Roles and Responsibilities
Clearly define the roles and responsibilities of each team member involved in quality control. This ensures that everyone understands their specific contributions and accountability.
Quality Manager: Responsible for overall quality management, ensuring that all procedures are followed.
Site Supervisors: Tasked with day-to-day oversight and immediate corrective actions.
Inspection Team: Conducts regular inspections and tests, and reports findings to the quality manager.
Subcontractors and Suppliers: Must adhere to the quality standards outlined in the plan and cooperate during inspections.
5. Risk Management and Contingency Planning
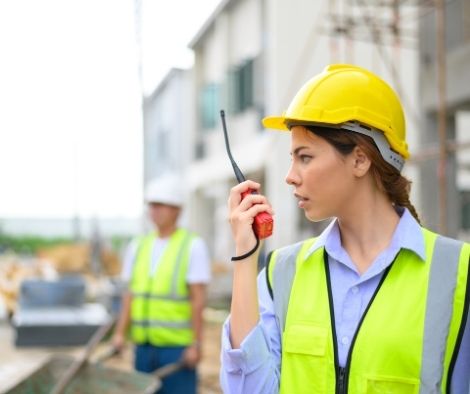
Integrate a robust risk management section to proactively address potential issues. This part of the plan should include:
Risk Identification: List potential risks related to quality, such as material defects, workmanship issues, or environmental factors.
Risk Analysis: Assess the likelihood and impact of each identified risk.
Mitigation Strategies: Develop strategies to reduce or eliminate risks.
Contingency Plans: Outline steps to be taken if a quality deviation occurs, including immediate corrective actions and long-term remedial measures.
6. Compliance with USACE/NAVFAC Standards
To meet the specialized requirements of USACE and NAVFAC, your plan must be explicitly aligned with their standards and guidelines.
Reference Documentation: Include references to the specific USACE and NAVFAC guidelines and standards that apply to your project.
Tailored Procedures: Adapt your quality control procedures to ensure they reflect the higher requirements expected by these agencies.
Approval Process: Detail the process for submitting and revising the quality control plan for review and approval by USACE/NAVFAC.
7. Training and Communication
Even the most detailed and technically accurate Quality Control Plan (QCP) will fall short if it’s not supported by robust training and consistent communication. Writing a QCP for approval isn’t just about checking compliance boxes—it’s about demonstrating how your company will actively maintain high-quality standards throughout the lifecycle of a project. That assurance comes alive through how your team is trained and how they communicate.
Training Programs: Empowering Your Team with Knowledge
A well-written QCP includes a section that clearly outlines your training strategy. This shows reviewers (like the U.S. Army Corps of Engineers or other contracting authorities) that your personnel are not only aware of the quality expectations—they’re equipped to meet them.
Key training areas to include:
Project-specific quality standards: Tailor your training to the specs of the job, so everyone—from field crew to QC Managers—knows what’s required.
Inspection techniques: Make sure your team understands what to look for and how to properly document and verify compliance.
Corrective actions and root cause analysis: Train personnel on how to handle deficiencies, communicate issues, and prevent repeat problems.
Onboarding for new hires: Show how new staff will be brought up to speed quickly and effectively.
Be specific about how often training happens, who conducts it, and how attendance and comprehension will be documented. This level of detail builds confidence in your plan.
8. Monitoring and Continuous Improvement
A dynamic quality control plan is one that adapts over time. Include mechanisms for monitoring performance and incorporating feedback to improve processes.
Performance Metrics: Define key performance indicators (KPIs) that will be tracked throughout the project.
Audit Schedules: Schedule regular internal and external audits to ensure ongoing compliance.
Feedback Mechanisms: Set up systems for capturing and analyzing feedback from all stakeholders, using this data to refine the quality control processes.
Benefits of a Well-Structured Quality Control Plan
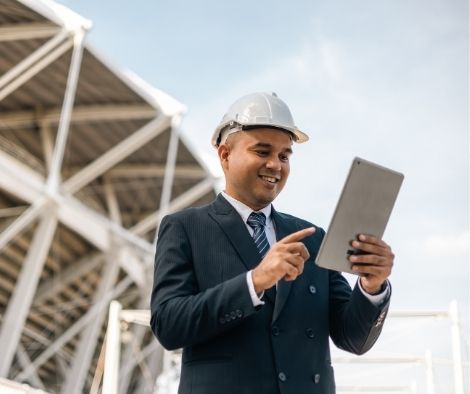
A strong Quality Control Plan (QCP) does far more than fulfill contract requirements—it serves as a foundational tool for operational excellence, team alignment, and long-term business success. When thoughtfully written and implemented, a QCP transforms project execution from reactive problem-solving to proactive precision. Here’s how:
Enhanced Project Efficiency
A well-structured QCP creates order, clarity, and accountability from day one.
Streamlined Processes:
Clear quality procedures provide a roadmap for every phase of construction. When teams know exactly what’s expected and how to execute it, workflow friction is minimized. This reduces downtime, eliminates redundant steps, and helps subcontractors and field crews stay on the same page.
Proactive Issue Resolution:
A strong QCP equips your team to catch small issues before they become big problems. Instead of waiting for defects or delays to show up at the final inspection, a real-time inspection and reporting process means problems are corrected early—saving both time and stress.
Cost Savings
Your QCP isn’t just a document—it’s a money-saving tool.
Reduced Rework:
Rework is one of the biggest hidden drains on any project. A detailed QCP minimizes errors by ensuring inspections, checklists, and approval checkpoints are baked into your process. Getting it right the first time reduces labor hours and material waste.
Improved Resource Management:
When quality control is baked into your scheduling and task execution, you avoid over-ordering, underutilizing, or misallocating materials. Manpower and materials are used more efficiently, allowing for better budget control and profit margins.
Increased Safety and Regulatory Compliance
Safety and quality go hand in hand—and a solid QCP supports both.
Stricter Adherence to Standards:
Whether you’re working under USACE, NAVFAC, DOT, or local jurisdiction requirements, a QCP helps ensure your project meets all applicable codes and contract specs. This reduces the risk of non-compliance, fines, or failed inspections.
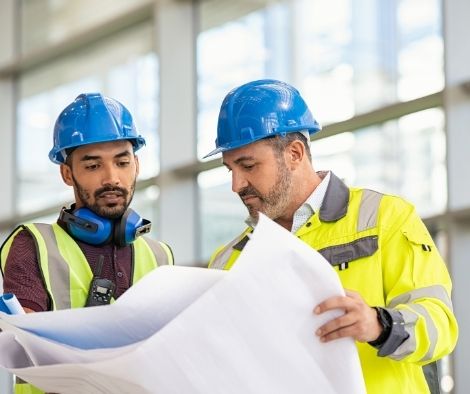
Better Risk Management:
By requiring daily reports, pre-task hazard analyses, and ongoing inspections, a QCP helps your team spot hazards early and respond with appropriate corrective measures. This means safer job sites and a lower chance of costly incidents or OSHA violations.
Higher Client Satisfaction
Quality control directly affects the client experience—from preconstruction to close-out.
Meeting Client Expectations:
When projects are delivered on time, within budget, and without quality defects, clients take notice. A strong QCP shows that your company is committed to excellence—not just lip service. This builds trust and increases your chances of repeat business.
Enhanced Reputation:
Word travels fast in the construction world. Companies known for delivering consistent, high-quality work gain a competitive edge. With fewer callbacks and cleaner punch lists, your team looks more professional—opening the door to larger contracts and more prestigious projects.
Implementing Your Quality Control Plan
Taking the step from planning to implementation is critical. Here’s a step-by-step guide to ensure your quality control plan is effectively put into practice:
Kick-Off Meeting:
Organize a meeting with all key stakeholders to review the quality control plan in detail. Ensure everyone understands their roles and the importance of adhering to the plan.Training and Orientation:
Conduct comprehensive training sessions focused on the plan’s procedures and quality standards. Make sure all team members, including subcontractors, are fully informed.Establish Monitoring Tools:
Set up digital platforms or software tools that allow for real-time monitoring of quality metrics. These tools should facilitate easy documentation and prompt reporting of any deviations.Regular Audits and Inspections:
Schedule regular audits to assess compliance with the plan. Use these audits as opportunities to gather feedback and identify areas for improvement.Feedback and Continuous Improvement:
Implement a system for collecting feedback from the field. Use this data to make ongoing adjustments to the quality control processes, ensuring they evolve with the project needs.Documentation and Reporting:
Maintain meticulous records of all inspections, audits, and corrective actions. This documentation is essential for both internal reviews and external regulatory inspections.
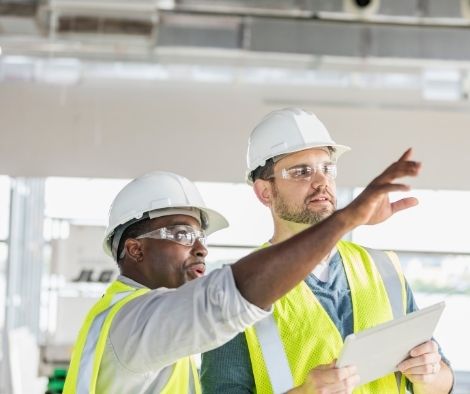
Final Thoughts
Many contractors take on quality control plans themselves, but it’s easy to run into challenges like rejections, lost time, and extra costs. After putting in so much effort, it can be frustrating when things don’t go as planned. We make sure the job gets done right the first time, saving you time, money, and headaches.
Don’t make that mistake. At Plan The Job, we take the guesswork out of the process by:
Assessing Your Project Needs: We carefully evaluate your project requirements to ensure compliance with USACE and NAVFAC standards.
Crafting a Custom Plan: Our experts design a tailored, thorough plan that addresses every regulatory guideline.
Ensuring Quality and Accuracy: We double-check every detail to eliminate errors and prevent costly rejections.
Providing Ongoing Support: We guide you through the submission process to ensure smooth, fast approvals.
Avoid Costly Rejections and Delays!
Get it right the first time with expert guidance that saves you time, money, and frustration. Contact us today for a Free, No-Obligation Expert Consultation and secure your federal contract with confidence!
📞 Call (941) 229-5200
📧 Email [email protected]
🔗 Get Your Free Quote Now.